Manufacturing has long been a cornerstone of the American economy, providing millions of jobs and driving technological innovation. The sector not only produces essential goods for domestic consumption but also plays a crucial role in U.S. exports. However, manufacturing employment has experienced significant shifts due to globalization, automation, and changing trade policies.
This research paper examines employment trends across different manufacturing subsectors, providing insights into workforce distribution, historical changes, and emerging challenges. Using data from the Bureau of Labor Statistics (BLS), we analyze employment figures, workforce trends, and the impact of economic and technological factors on the manufacturing labor market.
The goal of this report is to present a comprehensive understanding of where manufacturing jobs are concentrated, how they have evolved, and what challenges and opportunities lie ahead for American workers in this sector.
In a Nutshell
- Manufacturing employment peaked in 1979 with 19.6 million jobs, but by 2019, it had declined to 12.8 million, marking a 35% reduction over 40 years.
- As of December 2024, total U.S. manufacturing employment stands at approximately 12.8 million jobs, showing recent stabilization after decades of decline.
- The largest manufacturing employers by subsector are:
- Transportation Equipment Manufacturing: 1.8 million workers (14.1% of total manufacturing employment)
- Food Manufacturing: 1.6 million workers (12.5%)
- Fabricated Metal Product Manufacturing: 1.4 million workers (10.9%)
- Machinery Manufacturing: 1.1 million workers (8.6%)
- The hardest-hit industries by offshoring include apparel manufacturing, which declined from 900,000 jobs in the 1970s to just 70,000 today.
- Automation and robotics have reshaped the industry, with over 44,000 industrial robots installed in U.S. factories in 2022 alone.
- The U.S. could face a shortfall of 2.1 million manufacturing workers by 2030 due to the growing skills gap, potentially costing the economy $1 trillion in lost production.
- Trade policies have significantly impacted employment:
- The de minimis loophole allows over $800 billion worth of duty-free imports, hurting domestic manufacturers.
- The CHIPS and Science Act and Inflation Reduction Act (IRA) are projected to create tens of thousands of manufacturing jobs in semiconductors and clean energy.
- Geographic shifts in manufacturing:
- The Midwest still leads in employment, but Southern states like Tennessee, South Carolina, and Alabama are seeing faster growth.
- Small urban counties have driven 61% of new manufacturing job growth since 2019, while rural areas have collectively lost 20,000 jobs.
- Reshoring efforts are gaining momentum, with over 350,000 jobs brought back to the U.S. between 2010 and 2020 due to supply chain concerns and new policies.
Our Methodology
To analyze the state of American manufacturing jobs, we utilized data sets from the Bureau of Labor Statistics (BLS), specifically from the Current Employment Statistics (CES) and Occupational Employment and Wage Statistics (OEWS) programs. These sources provide detailed employment numbers, industry classifications, and wage trends.
Approach to Data Analysis
- Sector Categorization: We classified manufacturing jobs according to NAICS (North American Industry Classification System) codes, breaking down employment trends by subsector.
- Employment Trends: We examined historical employment data to identify long-term trends in job growth or decline across different industries.
- Regional Distribution: We analyzed geographic patterns to determine which states and regions have the highest concentration of manufacturing jobs.
- Technology and Policy Impact: We evaluated the effects of automation, trade policies, and workforce development programs on employment levels.
This methodology ensures a comprehensive understanding of the current state of U.S. manufacturing employment and its future trajectory.
Historical Trends in Manufacturing Employment
Manufacturing employment in the United States has experienced significant fluctuations over the past several decades. In June 1979, the sector reached its peak employment with approximately 19.6 million workers. However, by June 2019, this number had declined to about 12.8 million, marking a 35% reduction over 40 years.
Several factors have contributed to this decline:
- Automation and Technological Advancements: The integration of advanced technologies and automation has increased production efficiency but often at the expense of manual labor, leading to reduced demand for certain job roles.
- Globalization and Trade Policies: The rise of global trade, particularly following China’s entry into the World Trade Organization in 2001, introduced heightened competition. Many U.S. manufacturers relocated operations overseas to capitalize on lower labor costs, resulting in domestic job losses (wsj.com).
- Economic Recessions: Economic downturns have periodically impacted manufacturing employment. Notably, the early 2000s and the 2007–2009 Great Recession led to substantial job reductions in the sector.
Despite these challenges, there have been periods of recovery. For instance, post-2010 saw a resurgence in manufacturing jobs, driven by reshoring initiatives and increased demand for domestically produced goods. By December 2024, manufacturing employment stood at approximately 12.87 million, reflecting a stabilization in recent years.
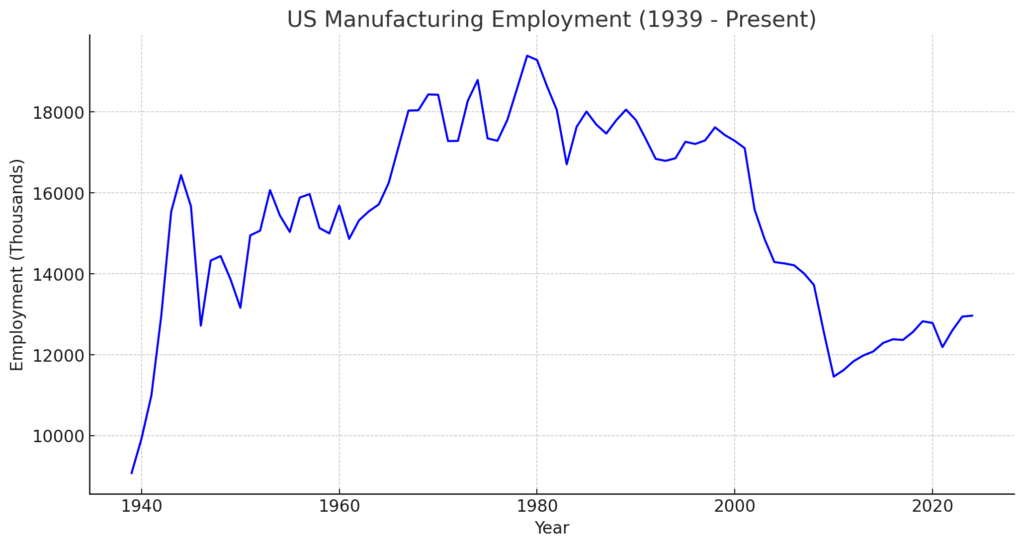
Source: bls.gov
Geographic Distribution of Manufacturing Jobs
Manufacturing employment in the United States is unevenly distributed, with certain states and regions serving as industrial hubs.
- Midwest: Often referred to as the “Rust Belt,” states like Indiana, Ohio, and Michigan have historically been manufacturing powerhouses. In 2013, Ohio employed approximately 662,100 manufacturing workers, ranking it among the top states for manufacturing employment (epi.org).
- South and Southeast: In recent decades, manufacturing growth has shifted towards the South and Southeast. States such as South Carolina, Tennessee, and Alabama have attracted industries like automotive and aerospace manufacturing, benefiting from favorable business climates and labor markets (bls.gov).
- West: States like California and Texas also have significant manufacturing sectors. In 2013, California led the nation with approximately 1,251,400 manufacturing jobs, while Texas had about 871,700 (epi.org).
Urban areas tend to concentrate manufacturing employment. As of 2010, approximately 79.5% of all manufacturing jobs were located in metropolitan areas, reflecting the advantages of urban infrastructure and access to skilled labor (brookings.edu).
However, recent trends indicate a shift. Post-2019, small urban counties have become significant drivers of manufacturing job growth, accounting for 61% of new manufacturing jobs added since 2019. Conversely, rural counties have experienced a decline, collectively losing about 20,000 manufacturing jobs in the same period (eig.org).
The Impact of Automation and Technology on Manufacturing Jobs
The manufacturing sector has undergone a dramatic transformation over the past few decades, driven by automation and rapid advancements in technology. While these developments have boosted efficiency and productivity, they have also displaced traditional jobs, forcing workers to adapt to new roles that require more specialized skills.
The Rise of Robotics
One of the most significant changes has been the rise of industrial robotics. In 2022 alone, U.S. manufacturers installed over 44,000 new industrial robots, an all-time high, according to the International Federation of Robotics. These machines, particularly prevalent in industries like automotive, electronics, and metal fabrication, have taken over tasks once performed by human workers. Automation has allowed manufacturers to increase output and maintain global competitiveness, but it has also led to job restructuring. Instead of traditional assembly line workers, companies now seek robotics engineers, AI specialists, and technicians capable of maintaining complex systems.
3D Printing and Smart Technology
Beyond robotics, the introduction of 3D printing and smart factory technology has reshaped manufacturing processes. Additive manufacturing, commonly known as 3D printing, has enabled manufacturers to create components with greater precision, less waste, and lower costs. Meanwhile, the emergence of smart factories—where Internet of Things (IoT) devices track performance and optimize production—has further reduced reliance on manual labor. These advancements are reshaping supply chains, allowing companies to operate with leaner workforces while simultaneously creating demand for highly skilled technicians and analysts.
The Skill Gap
Despite the widespread adoption of automation, the industry still faces an acute skills gap. The National Association of Manufacturers (NAM) estimates that by 2030, over 2.1 million manufacturing jobs could go unfilled due to a shortage of qualified workers. While automation has eliminated many routine jobs, it has also created new, higher-paying opportunities in fields such as robotics programming, data analytics, and machine maintenance. However, many workers lack the training needed to transition into these roles, creating a pressing need for apprenticeship programs, vocational training, and industry partnerships with technical schools.
Ultimately, while technology is not eliminating manufacturing jobs outright, it is fundamentally changing the nature of work in the sector. The workforce of the future must be more adaptable, technically skilled, and prepared for a digital-first manufacturing environment. Without significant investments in workforce training, the U.S. risks falling behind in the global race for advanced manufacturing dominance.
The Role of Trade Policy and Globalization in Manufacturing Jobs
Few factors have influenced the trajectory of American manufacturing employment as profoundly as trade policy and globalization. Over the past several decades, the outsourcing of jobs, international trade agreements, and shifting economic priorities have altered the structure of the domestic manufacturing workforce, leaving some industries decimated while others have thrived.
The Rush to China
The most significant turning point came in 2001 when China joined the World Trade Organization (WTO). Almost immediately, American manufacturers, particularly in apparel, textiles, and consumer electronics, faced overwhelming competition from low-cost Chinese producers. Seeking to cut costs, many companies moved their operations overseas, resulting in the loss of over 3.7 million U.S. manufacturing jobs between 2001 and 2018, according to the Economic Policy Institute (EPI). The damage was particularly severe in the Rust Belt, where factory closures devastated communities that had long depended on manufacturing as their economic backbone.
Reshoring Initiative
However, recent years have seen a shift in momentum. Concerns over supply chain vulnerabilities, national security, and economic resilience have led to a push for reshoring—bringing manufacturing jobs back to the U.S. The Reshoring Initiative reported that more than 350,000 manufacturing jobs were reshored between 2010 and 2020, particularly in automotive, medical equipment, and electronics. The COVID-19 pandemic further underscored the risks of over-reliance on foreign supply chains, prompting companies and policymakers alike to rethink offshoring strategies.
Trade Agreements and Tariffs
Trade agreements and tariffs have also played a decisive role in shaping manufacturing employment. The U.S.-Mexico-Canada Agreement (USMCA), which replaced NAFTA in 2020, introduced stricter regional content requirements, incentivizing manufacturers to source materials from North America rather than from overseas suppliers. Meanwhile, tariffs imposed on Chinese imports during the Trump administration, and largely maintained under Biden, have had a mixed impact. While they have encouraged some companies to increase domestic production, they have also raised costs for manufacturers reliant on imported components.
The De Minimis Loophole
A more subtle but equally consequential issue is the de minimis loophole, which allows foreign sellers to ship goods valued under $800 per package duty-free into the United States. This policy has given a competitive edge to Chinese e-commerce giants like Shein and Temu, whose low-cost products flood the U.S. market without the same tax and regulatory burdens faced by domestic manufacturers. American businesses have increasingly pushed for reform, arguing that this loophole creates an uneven playing field that undermines domestic production.
Looking Ahead
Looking ahead, industrial policies such as the CHIPS and Science Act and the Inflation Reduction Act (IRA) are expected to play a crucial role in revitalizing American manufacturing. These policies aim to strengthen domestic production in critical sectors such as semiconductors, clean energy, and rare earth materials, reducing reliance on foreign supply chains while creating high-quality manufacturing jobs.
While globalization has led to significant job losses in certain sectors, the momentum is now shifting toward rebuilding domestic production capabilities. Future trade policies, along with potential de minimis reforms, will determine whether the U.S. manufacturing sector continues its slow recovery or remains vulnerable to foreign competition.
Workforce Challenges and Future Outlook
Despite signs of stabilization in manufacturing employment, the sector faces several persistent challenges that could determine its trajectory in the coming decades. Workforce shortages, the skills gap, and the need for stronger education and training pipelines are among the most pressing concerns.
Shortage of Skilled Workers
One of the most significant challenges is the shortage of skilled workers. While automation has reduced the demand for some traditional factory roles, it has also increased the need for technicians, engineers, and specialists who can operate and maintain advanced manufacturing systems. The National Association of Manufacturers (NAM) projects that by 2030, the U.S. could face a shortfall of 2.1 million manufacturing workers, potentially costing the economy up to $1 trillion in lost production.
This shortage is partly driven by demographic shifts. As older workers retire, there are fewer young workers entering manufacturing careers. A 2021 Deloitte and Manufacturing Institute study found that 77% of manufacturers struggle to attract and retain workers, despite offering competitive wages and benefits. The perception of manufacturing as a low-tech, outdated career path continues to deter many potential workers, even as the sector evolves into one of the most technologically advanced industries.
More Training Programs
To combat these challenges, manufacturers and policymakers are expanding apprenticeship programs and vocational training. Companies are increasingly partnering with community colleges and technical schools to develop specialized training programs. Some initiatives, such as the Federation for Advanced Manufacturing Education (FAME) program, offer hands-on training designed to equip students with automation, robotics, and advanced machining skills.
Impact of Government Policy
Another critical factor shaping the future of manufacturing employment is government policy and investment in domestic production. Recent legislation, including the CHIPS and Science Act and the Inflation Reduction Act (IRA), is expected to create tens of thousands of new manufacturing jobs, particularly in semiconductor fabrication, electric vehicle production, and clean energy sectors. These investments represent a shift toward onshoring strategic industries, reducing reliance on foreign supply chains, and positioning the U.S. as a global leader in high-tech manufacturing.
However, the success of these efforts will depend on the ability to attract, train, and retain workers who can meet the demands of a rapidly evolving industry. If the workforce shortage persists, manufacturers may struggle to fully capitalize on the growing domestic demand for American-made goods.
Employment Analysis by Manufacturing Subsectors
Manufacturing is a vast and diverse sector encompassing numerous industries, each with distinct employment trends. While some subsectors have seen significant declines due to offshoring and automation, others have demonstrated resilience and growth.
Subsector | Employment (Thousands) | Percentage of Total Manufacturing Employment |
---|---|---|
Food Manufacturing | 1,600 | 12.5% |
Beverage and Tobacco Product Manufacturing | 230 | 1.8% |
Textile Mills | 90 | 0.7% |
Textile Product Mills | 100 | 0.8% |
Apparel Manufacturing | 70 | 0.5% |
Leather and Allied Product Manufacturing | 30 | 0.2% |
Wood Product Manufacturing | 400 | 3.1% |
Paper Manufacturing | 340 | 2.7% |
Printing and Related Support Activities | 400 | 3.1% |
Petroleum and Coal Products Manufacturing | 110 | 0.9% |
Chemical Manufacturing | 800 | 6.3% |
Plastics and Rubber Products Manufacturing | 600 | 4.7% |
Nonmetallic Mineral Product Manufacturing | 400 | 3.1% |
Primary Metal Manufacturing | 350 | 2.7% |
Fabricated Metal Product Manufacturing | 1,400 | 10.9% |
Machinery Manufacturing | 1,100 | 8.6% |
Computer and Electronic Product Manufacturing | 1,000 | 7.8% |
Electrical Equipment, Appliance, and Component Manufacturing | 400 | 3.1% |
Transportation Equipment Manufacturing | 1,800 | 14.1% |
Furniture and Related Product Manufacturing | 350 | 2.7% |
Miscellaneous Manufacturing | 600 | 4.7% |
Total Manufacturing Employment | 12,800 | 100% |
Food Manufacturing (NAICS 311)
The food manufacturing subsector remains one of the largest and most stable industries within U.S. manufacturing, employing approximately 1.6 million workers as of 2024. Unlike other manufacturing industries that have faced sharp declines due to offshoring, food production has maintained a relatively strong domestic presence. The necessity of perishable goods processing, local supply chains, and regulatory compliance has kept much of the industry rooted in the U.S.
Employment Trends
According to Bureau of Labor Statistics (BLS) data, employment in food manufacturing has seen steady growth over the past three decades, as illustrated in the accompanying graph. Since 1990, the number of employees in the subsector has gradually increased, reflecting population growth, increased demand for processed foods, and technological advancements that have enhanced production efficiency.
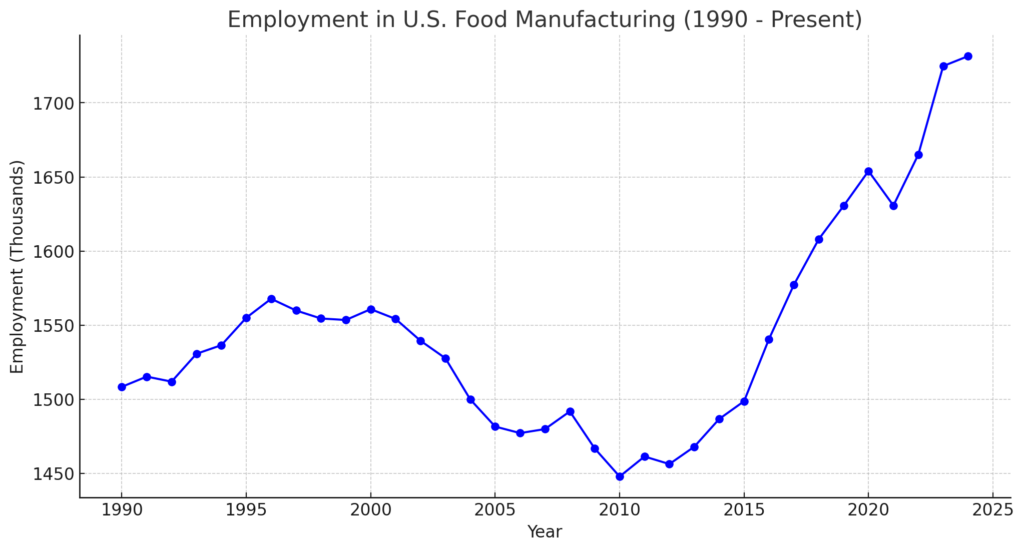
Key Industries and Workforce Composition
Food manufacturing encompasses a wide range of sub-industries, including:
- Meat and poultry processing, which remains the largest employer within the subsector, accounting for nearly 500,000 jobs nationwide.
- Dairy product manufacturing, which employs approximately 120,000 workers, with major hubs in Wisconsin, California, and Pennsylvania.
- Grain and bakery product manufacturing, which provides over 250,000 jobs, supplying both domestic and global markets.
- Beverage manufacturing, including soft drinks, breweries, and wineries, has seen strong growth in craft and specialty production, creating new employment opportunities.
Impact of Automation and Workforce Challenges
Like many other manufacturing subsectors, food production is experiencing a shift due to automation and robotics. Large-scale food processors have increasingly integrated automated sorting, packaging, and quality control systems, reducing the demand for low-skill, repetitive labor while increasing the need for technicians and maintenance specialists who can operate and troubleshoot these technologies.
However, the industry faces workforce shortages in key roles, particularly in meatpacking and food processing plants, where labor-intensive work and difficult conditions have led to high turnover rates. The COVID-19 pandemic further exposed vulnerabilities in the sector, with supply chain disruptions and temporary plant closures highlighting the need for greater workforce protections and improved automation to maintain production stability.
Geographic Distribution
Food manufacturing employment is concentrated in agricultural and high-consumption states, including:
- California, the nation’s largest food producer, with major hubs in Fresno, Modesto, and Los Angeles.
- Texas, where food processing plants employ thousands, particularly in Houston and Dallas.
- Iowa, Nebraska, and Kansas, where meatpacking and grain processing are dominant employers.
Future Outlook
The food manufacturing subsector is expected to continue growing, driven by consumer demand for processed and convenience foods, supply chain resiliency efforts, and advancements in food safety and preservation technology. While automation will likely replace some traditional roles, it will also create new jobs in equipment maintenance, food science, and quality control.
Additionally, sustainability trends and the demand for organic, plant-based, and alternative protein products may lead to new opportunities for job creation, particularly in emerging food tech industries. Policymakers and industry leaders must focus on workforce training, food safety innovation, and supply chain enhancements to ensure continued stability and growth in this critical sector.
Beverage and Tobacco Product Manufacturing (NAICS 312)
The Beverage and Tobacco Product Manufacturing subsector encompasses establishments that manufacture beverages (both alcoholic and non-alcoholic) and tobacco products. This sector plays a significant role in the U.S. economy, contributing to both employment and gross domestic product (GDP).
Employment Trends
As of the latest data, the subsector employs approximately 335,100 workers. The employment distribution within this sector includes various occupations, with notable numbers in roles such as:
- Packaging and Filling Machine Operators and Tenders: Approximately 26,090 employees
- Laborers and Freight, Stock, and Material Movers, Hand: Around 11,930 employees
- Sales Representatives, Wholesale and Manufacturing (Except Technical and Scientific Products): About 14,340 employees
These roles are essential in ensuring the efficient production, packaging, and distribution of beverage and tobacco products across the nation.
Industry Composition
The subsector is divided into two primary industries:
- Beverage Manufacturing: This includes the production of soft drinks, bottled water, breweries, wineries, and distilleries.
- Tobacco Manufacturing: This involves the processing of tobacco into products such as cigarettes, cigars, and smokeless tobacco.
Economic Impact
In 2024, the Beverage and Tobacco Product Manufacturing industry reported sales of approximately $228.6 billion, reflecting its substantial contribution to the U.S. economy.
Challenges and Trends
The industry faces several challenges and evolving trends:
- Health and Wellness Movement: There is a growing consumer preference for healthier beverage options, leading to increased demand for non-alcoholic and low-sugar beverages.
- Regulatory Environment: The sector is subject to stringent regulations, especially concerning tobacco products, which can impact production and marketing strategies.
- Technological Advancements: Automation and advanced manufacturing processes are being adopted to enhance efficiency and meet changing consumer demands.
Future Outlook
The Beverage and Tobacco Product Manufacturing subsector is expected to continue adapting to consumer preferences and regulatory changes. The emphasis on health-conscious products and sustainable practices will likely drive innovation and influence employment trends within the industry.
Textile Mills (NAICS 313) and Textile Product Mills (NAICS 314)
The Textile Mills (NAICS 313) and Textile Product Mills (NAICS 314) subsectors have historically played a significant role in U.S. manufacturing. However, these industries have faced substantial job losses due to automation, globalization, and shifting trade policies. Once a dominant employer in states like North Carolina, South Carolina, and Georgia, employment in these subsectors has declined dramatically over the past three decades.
Employment Trends
As illustrated in the accompanying graph, employment in Textile Mills has experienced a long-term decline since 1990. In the early 1990s, textile mill employment stood at over 600,000 workers, but by 2024, it had fallen to approximately 90,000. This 85% decline reflects the combined impact of offshoring, automation, and increased reliance on imported textiles.
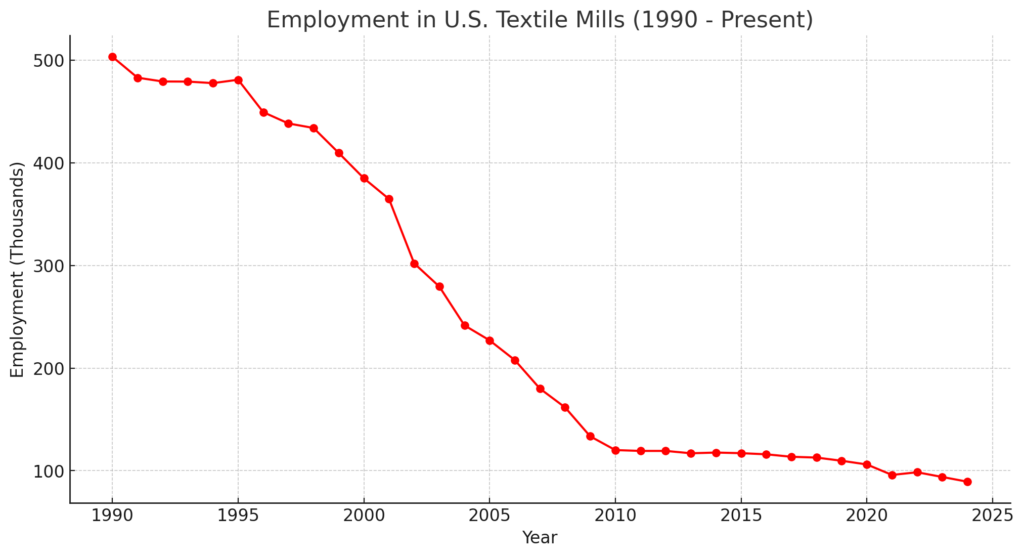
Meanwhile, the Textile Product Mills subsector, which includes the production of household furnishings, carpets, and industrial textiles, has also faced challenges but has retained a slightly more stable workforce. This subsector currently employs around 100,000 workers, a decline from its peak in the 1980s but not as steep as the job losses seen in textile mills.
Industry Composition
The Textile Mills subsector primarily involves fiber preparation, spinning, weaving, and knitting to create raw textile materials. The key industries within this subsector include:
- Cotton and Synthetic Fiber Mills – Focused on producing raw fabric and yarn.
- Knitting Mills – Responsible for producing knitted fabrics and hosiery.
- Finishing and Coating Mills – Where fabric undergoes bleaching, dyeing, and finishing.
The Textile Product Mills subsector, on the other hand, focuses on manufacturing end-use textile products, such as:
- Carpets and Rugs
- Household and Institutional Furnishings (curtains, bed linens, towels)
- Industrial Textile Products (protective fabrics, filtration materials, and upholstery)
Factors Behind Declining Employment
Several key factors have contributed to the significant job losses in these subsectors:
- Trade Liberalization and Offshoring
- The passage of NAFTA (1994) and China’s entry into the WTO (2001) led to a sharp increase in textile and apparel imports, particularly from China, India, and Vietnam.
- U.S. textile production shifted offshore to take advantage of lower labor costs, leading to widespread mill closures.
- Automation and Technological Advancements
- Modern textile mills require fewer workers as advanced spinning, weaving, and dyeing technologies have increased efficiency.
- Robotics and AI-driven textile manufacturing processes have further reduced the demand for manual labor.
- Changing Consumer Demand
- The rise of fast fashion has favored low-cost, mass-produced fabrics, often sourced from overseas.
- However, demand for sustainable, eco-friendly textiles has begun to create niche opportunities for domestic manufacturers.
Geographic Distribution
Despite job losses, the U.S. still maintains a textile manufacturing presence, with North Carolina, South Carolina, and Georgia remaining key hubs for textile production.
- North Carolina leads in the production of synthetic fibers and textile research.
- South Carolina and Georgia are major players in carpet and rug manufacturing, particularly in Dalton, GA, known as the “Carpet Capital of the World.”
Future Outlook
While textile manufacturing in the U.S. is unlikely to return to its peak employment levels, there are emerging opportunities for growth and innovation in the sector:
- Reshoring Initiatives – Some manufacturers are shifting production back to the U.S. to reduce reliance on global supply chains.
- Sustainable Textiles – The rise of organic, recycled, and biodegradable fabrics is creating demand for domestic eco-friendly textile production.
- Advanced Textiles – Innovations in protective fabrics, smart textiles, and nanotechnology may open new markets for high-tech U.S. textile manufacturers.
The Textile Mills and Textile Product Mills subsectors have undergone major transformations, shifting from labor-intensive production to leaner, more automated facilities. While global competition and technological shifts have significantly reduced employment, niche markets, sustainability trends, and reshoring efforts may provide opportunities for job stabilization and growth in the years ahead.
Apparel Manufacturing (NAICS 315)
The Apparel Manufacturing subsector has been one of the most impacted industries within U.S. manufacturing, experiencing severe job losses over the past several decades. Historically, the United States was a global leader in apparel production, but offshoring, automation, and trade policy changes have drastically reduced employment in the sector. Today, most clothing sold in the U.S. is imported, primarily from China, Vietnam, Bangladesh, and Mexico.
Employment Trends
As illustrated in the accompanying graph, employment in Apparel Manufacturing has plummeted over the past three decades. In 1990, the sector employed nearly 900,000 workers, but by 2024, employment had dropped to just 70,000, reflecting a 92% decline. This dramatic reduction is largely due to offshoring of labor-intensive garment production to lower-wage countries and the rise of fast fashion.
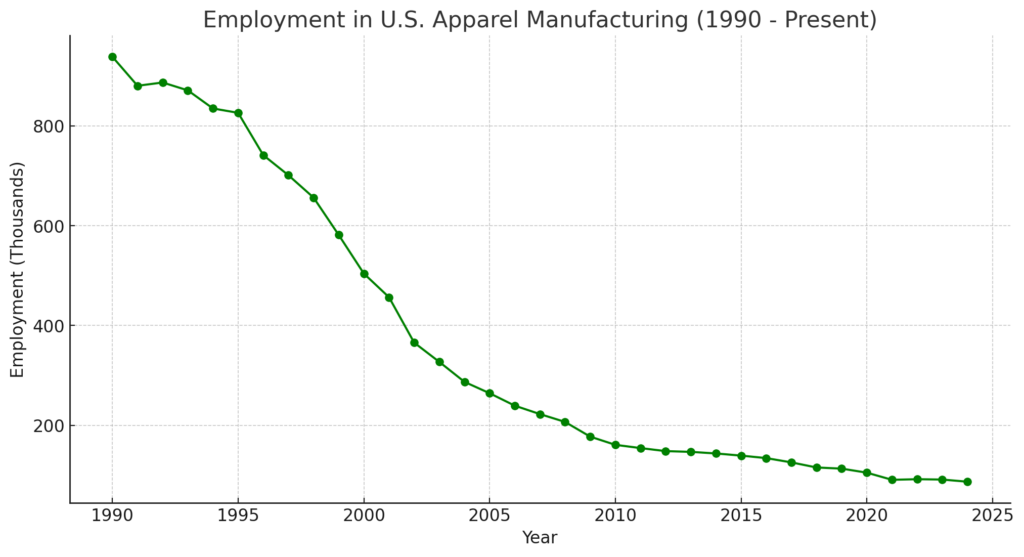
Industry Composition
The Apparel Manufacturing subsector is composed of three primary industries:
- Cut and Sew Apparel Manufacturing – The largest segment, producing garments from purchased fabric.
- Apparel Knitting Mills – Focused on knitting fabric and manufacturing knit garments.
- Apparel Accessories and Other Apparel Manufacturing – Includes hats, gloves, belts, and specialized clothing.
Despite the steep decline in employment, niche markets and automation are shaping a new wave of domestic apparel production.
Key Factors Behind Declining Employment
- Offshoring and Trade Policies
- NAFTA (1994) and China’s entry into the WTO (2001) significantly impacted the sector by eliminating tariffs on foreign-made clothing, making imports cheaper than domestic production.
- The U.S. now imports over 97% of its apparel, primarily from low-cost labor markets in Asia and Latin America.
- The de minimis loophole, which allows foreign retailers to ship small packages duty-free, has benefited online fashion giants like Shein and Temu, further harming domestic apparel manufacturers.
- Automation and Technological Disruptions
- Sewing automation technology has advanced, but human labor is still required for intricate stitching and finishing.
- Robotics and AI-driven fabric cutting have increased efficiency, but automation has not fully offset the cost advantages of offshore labor.
- Rise of Fast Fashion
- Companies like Zara, H&M, and Shein have pioneered rapid, low-cost production cycles, making it difficult for U.S. manufacturers to compete on price.
- The consumer shift toward ultra-fast fashion has favored international mass-production hubs over higher-cost American apparel factories.
Geographic Distribution
Despite the decline, some U.S. regions remain apparel manufacturing hubs:
- California (Los Angeles area) – Specializes in high-end fashion, denim, and boutique manufacturing.
- New York (New York City) – Home to custom, high-fashion, and designer apparel production.
- North Carolina & South Carolina – Focus on hosiery, knitwear, and performance apparel.
Future Outlook
While large-scale U.S. apparel manufacturing is unlikely to return, certain trends may create opportunities for domestic production:
- Reshoring of high-tech, automated apparel production: Companies investing in robotic sewing machines and AI-driven supply chains may revive limited domestic production.
- Growth in sustainable, ethical fashion: Consumers are increasingly seeking “Made in USA” sustainable apparel, boosting demand for smaller-scale domestic production.
- Tariff policies and trade reforms: Possible changes to the de minimis loophole and trade agreements could help level the playing field for U.S. apparel manufacturers.
The Apparel Manufacturing subsector has suffered massive job losses, with most production moving offshore due to lower labor costs and trade liberalization. However, technology, sustainability initiatives, and reshoring efforts could create a revitalized, though smaller, domestic apparel industry focused on high-quality, automated production.
Leather and Allied Product Manufacturing (NAICS 316)
Similar to apparel, leather manufacturing has contracted significantly. Many jobs have shifted overseas, leaving the subsector with fewer than 30,000 employees nationwide. High-end leather goods, however, continue to see steady demand, supporting domestic production in small-scale operations.
Industry Composition
The subsector is divided into three primary industry groups:
- Leather and Hide Tanning and Finishing (NAICS 3161): This industry involves transforming raw hides into durable leather through processes like tanning, currying, and finishing.
- Footwear Manufacturing (NAICS 3162): Establishments in this group manufacture footwear from various materials, including leather, rubber, and plastics.
- Other Leather and Allied Product Manufacturing (NAICS 3169): This category includes the production of leather goods such as luggage, handbags, personal leather goods, and other miscellaneous items.
Employment Trends
As of 2023, the Leather and Allied Product Manufacturing subsector employed approximately 11,030 workers across various occupations. Notable roles within the industry include:
- Sewing Machine Operators: Approximately 2,070 employees.
- Shoe and Leather Workers and Repairers: Around 5,100 employees.
- Team Assemblers: About 2,250 employees.
- First-Line Supervisors/Managers of Production and Operating Workers: Approximately 1,200 employees.
- Inspectors, Testers, Sorters, Samplers, and Weighers: Around 410 employees.
Wage Information
In 2023, wage data for common occupations in this subsector were as follows:
- First-Line Supervisors/Managers of Production and Operating Workers: Median hourly wage of $24.15; annual median wage of $50,230.
- Sewing Machine Operators: Median hourly wage of $16.88; annual median wage of $35,110.
- Shoe and Leather Workers and Repairers: Median hourly wage of $16.73; annual median wage of $34,790.
- Team Assemblers: Median hourly wage of $17.30; annual median wage of $35,990.
- Inspectors, Testers, Sorters, Samplers, and Weighers: Median hourly wage of $16.51; annual median wage of $34,350.
Workplace Safety
The industry reported the following rates of workplace injuries and illnesses per 100 full-time workers in 2023:
- Total Recordable Cases: 3.4
- Cases Involving Days Away from Work, Job Restriction, or Transfer: 2.1
- Cases Involving Days Away from Work: 0.9
- Cases Involving Days of Job Transfer or Restriction: 1.2
Economic Indicators
The Producer Price Index (PPI) for the Leather and Allied Product Manufacturing industry showed the following changes in late 2024:
- September 2024: PPI at 205.356
- October 2024: PPI increased by 0.3% to 205.940
- November 2024: PPI increased by 0.3% to 206.638
- December 2024: PPI decreased by 0.2% to 206.320
Challenges and Trends
The Leather and Allied Product Manufacturing industry faces several challenges and evolving trends:
- Global Competition: The industry contends with significant competition from countries with lower production costs, impacting domestic manufacturing.
- Sustainability: There is a growing emphasis on sustainable and ethical sourcing of materials, influencing production processes and consumer preferences.
- Technological Advancements: Adoption of advanced manufacturing technologies aims to improve efficiency and product quality.
- Consumer Preferences: Shifts in consumer preferences toward synthetic and alternative materials are influencing product offerings within the industry.
Future Outlook
The Leather and Allied Product Manufacturing subsector is expected to continue adapting to global competition, technological advancements, and changing consumer preferences. Emphasis on sustainability and ethical practices may drive innovation and influence employment trends within the industry.
Wood Product Manufacturing (NAICS 321)
The Wood Product Manufacturing subsector plays a critical role in U.S. manufacturing, producing a wide range of products, including lumber, plywood, veneer, and engineered wood products. This sector supplies the construction, furniture, and paper industries, making it a foundational component of the American economy.
Employment Trends
Employment in Wood Product Manufacturing has fluctuated over the past several decades, influenced by housing market cycles, automation, and international competition. In 1990, the sector employed over 600,000 workers, but that number steadily declined due to the offshoring of furniture production, automation in sawmills, and economic downturns.
The Great Recession (2007-2009) had a particularly devastating impact on employment, as demand for housing plummeted. Employment dropped sharply from over 550,000 in 2007 to around 350,000 by 2010. The sector has since rebounded somewhat, tracking the housing market’s recovery. As of 2024, employment stands at approximately 400,000 workers, reflecting moderate growth but still well below historical peaks.
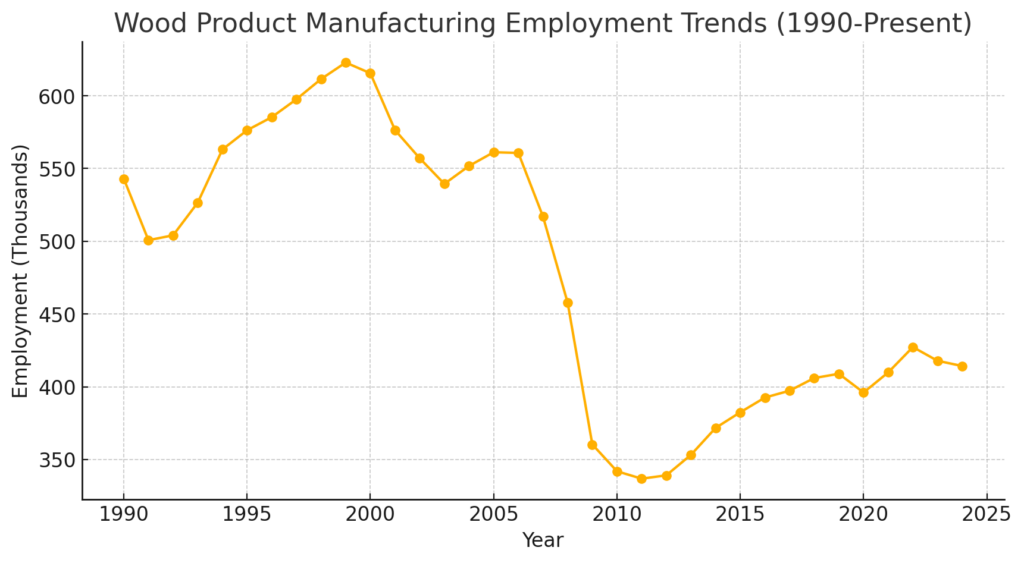
Industry Composition
The Wood Product Manufacturing sector is divided into three major categories:
- Sawmills and Wood Preservation (NAICS 3211)
- Involves cutting raw timber into lumber and treating wood products for durability.
- Supplies the construction and furniture industries.
- Faces increasing automation, reducing the need for manual labor.
- Veneer, Plywood, and Engineered Wood Product Manufacturing (NAICS 3212)
- Produces plywood, particleboard, laminated wood, and structural wood products.
- Growth driven by the rise of engineered wood in construction and furniture.
- Other Wood Product Manufacturing (NAICS 3219)
- Includes wood windows, doors, flooring, cabinetry, and millwork.
- Heavily impacted by trends in home renovation and new housing construction.
Technology and Automation in Wood Manufacturing
Like other manufacturing industries, wood product manufacturing has embraced automation to improve efficiency. Sawmills and wood processing plants now rely heavily on robotic saws, laser-guided cutting technology, and computer-controlled processing to optimize wood yields and reduce waste. These advancements have increased output but have also reduced the number of low-skill manual jobs in the sector.
3D printing with wood-based composites and cross-laminated timber (CLT) technology are also emerging as game changers in the industry. CLT is being promoted as a sustainable alternative to steel and concrete in construction, potentially driving growth in domestic wood production.
Workforce Challenges
The sector faces a significant labor shortage, particularly in skilled positions such as machine operators, maintenance technicians, and millwrights. The aging workforce is another concern, as a large percentage of experienced workers are nearing retirement without enough young workers entering the field.
- Workforce Shrinkage: The U.S. Bureau of Labor Statistics (BLS) projects only modest job growth in wood manufacturing over the next decade, largely due to automation.
- Skills Gap: Modern sawmills and engineered wood facilities require technically skilled workers, but vocational training programs in wood manufacturing are limited.
- Safety Concerns: The industry has one of the highest injury rates in U.S. manufacturing, leading to challenges in attracting new workers.
Geographic Distribution
Wood manufacturing employment is concentrated in forested regions of the U.S., particularly in:
- Pacific Northwest (Oregon, Washington, Idaho) – Home to the largest sawmill operations in the country.
- Southeastern U.S. (North Carolina, Georgia, Alabama) – A hub for engineered wood products and furniture manufacturing.
- Midwest (Wisconsin, Michigan, Minnesota) – Strong in veneer and plywood production.
Future Outlook
The future of wood product manufacturing will be shaped by several key trends:
- Housing Market Trends
- As long as demand for housing remains strong, wood production will remain steady.
- The rise of modular and prefabricated homes could increase demand for engineered wood products.
- Sustainability and Green Building
- Cross-laminated timber (CLT) is expected to drive demand for eco-friendly building materials.
- Sustainable forestry practices and carbon sequestration initiatives could benefit domestic wood producers.
- Automation and Reshoring
- Increased automation may allow some furniture and millwork production to return from overseas.
- Domestic production could see growth due to supply chain concerns and “Made in USA” consumer preferences.
- Workforce Development
- Investment in vocational training and apprenticeship programs will be essential for the sector to remain competitive.
- More automation will shift jobs toward higher-skill technical roles, creating opportunities for workers with advanced training.
Wood Product Manufacturing remains a key sector in U.S. manufacturing, supporting construction, furniture, and packaging industries. While automation and foreign competition have reduced employment over the decades, emerging trends in green building, engineered wood, and supply chain resilience could create new opportunities. However, addressing workforce shortages and safety concerns will be crucial for ensuring a strong future for the industry.
Paper Manufacturing (NAICS 322)
The Paper Manufacturing subsector is a vital part of U.S. manufacturing, producing a wide range of products including printing paper, packaging materials, tissues, and industrial paper products. Despite its importance, the industry has faced significant employment declines due to digitization, automation, and shifting global trade patterns.
Employment Trends
Employment in the Paper Manufacturing sector has steadily declined since 1990, when the industry employed over 640,000 workers. By 2024, employment had fallen to approximately 340,000, reflecting a 47% decrease over the past three decades.
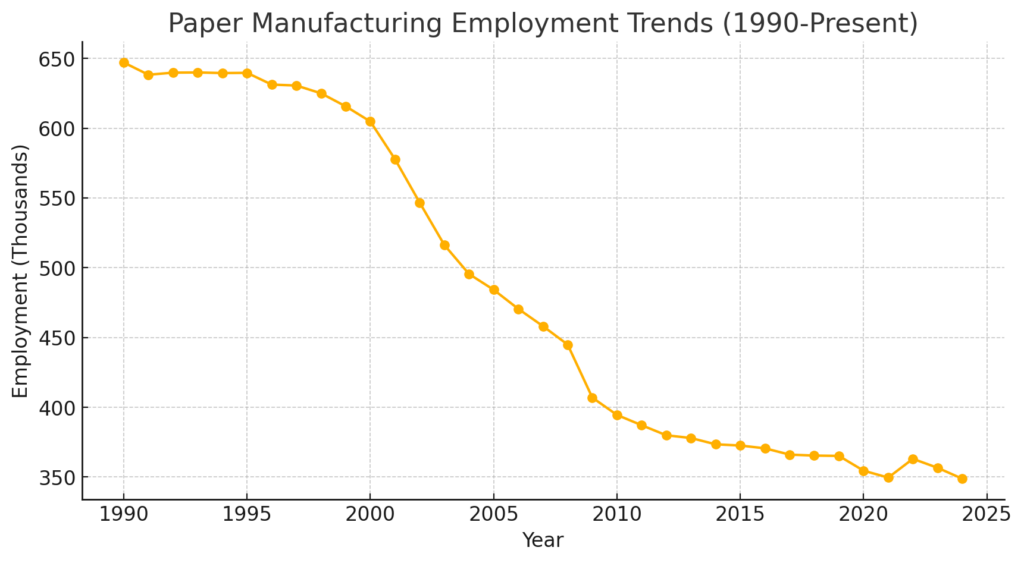
Several factors have contributed to this decline:
- The rise of digital media has reduced demand for printing and writing paper.
- Automation and consolidation in paper mills have reduced the need for manual labor.
- The offshoring of paper production to lower-cost countries, particularly in Asia and South America.
- Increased emphasis on sustainability, leading to a shift toward recycled materials and alternative packaging solutions.
Despite the overall decline, certain segments—such as packaging and hygiene products—have remained stable or grown due to rising e-commerce demand and consumer trends.
Industry Composition
The Paper Manufacturing sector is divided into two primary categories:
- Pulp, Paper, and Paperboard Mills (NAICS 3221)
- Involves the production of raw paper materials from wood pulp and recycled fibers.
- Supplies industries including publishing, packaging, and personal care products.
- Has seen a decline in employment due to automation and mill closures.
- Converted Paper Product Manufacturing (NAICS 3222)
- Produces finished products such as cardboard, paper bags, sanitary paper products, and stationery.
- Less impacted by digitization compared to pulp and paper mills, as demand for packaging and hygiene products remains strong.
Technology and Automation in Paper Manufacturing
Like other industrial sectors, Paper Manufacturing has embraced automation to increase efficiency and reduce production costs. Modern paper mills utilize:
- Automated conveyor systems for material handling.
- AI-driven quality control to detect imperfections in paper products.
- Energy-efficient pulping and drying technologies to minimize waste and environmental impact.
These advancements have led to fewer low-skill jobs in paper mills but have increased demand for highly skilled machine operators and technicians.
Workforce Challenges
Despite job losses in traditional roles, the industry still faces workforce challenges, particularly in retaining and training skilled employees. Key workforce issues include:
- Aging workforce: A significant portion of experienced paper mill workers are retiring, and fewer younger workers are entering the field.
- Technical skills gap: Modern paper mills require specialized knowledge in automation, machinery maintenance, and quality control.
- High energy and environmental costs: Stringent environmental regulations require workers with expertise in sustainable manufacturing and waste management.
Geographic Distribution
Paper manufacturing jobs are concentrated in states with strong forestry industries and access to major transportation routes, including:
- Wisconsin – The nation’s largest paper-producing state, home to major mills.
- Georgia – A key player in pulp and paperboard production.
- Maine and South Carolina – Significant hubs for wood pulp and printing paper.
- Washington and Oregon – Important for high-volume paper and packaging production.
Future Outlook
Despite long-term employment declines, certain factors could stabilize or revive segments of the industry:
- Growth in E-commerce Packaging
- Demand for corrugated boxes and sustainable packaging has surged due to e-commerce.
- Companies are shifting toward biodegradable and recyclable materials, opening opportunities for domestic paper manufacturers.
- Sustainability and Recycling Innovations
- Increasing emphasis on circular economy models and the use of recycled paper fibers could boost U.S. paper mills.
- Government regulations encouraging plastic-to-paper transitions in packaging and food service could benefit the industry.
- Onshoring and Supply Chain Resilience
- The COVID-19 pandemic exposed vulnerabilities in global supply chains, leading to reshoring efforts in critical manufacturing industries.
- U.S. paper producers could regain market share as companies seek domestic suppliers for essential goods like tissue paper and cardboard.
- Advanced Paper Products
- The rise of high-performance engineered paper for use in electronics, medical applications, and industrial packaging could drive growth.
- Research into nanocellulose technology (strong, lightweight materials derived from wood fibers) could create new high-tech jobs in the sector.
The Paper Manufacturing subsector has faced decades of job losses due to digitization, automation, and global competition. However, emerging trends in sustainable packaging, recycling innovations, and supply chain resilience may provide opportunities for the industry to stabilize and grow in select segments.
Moving forward, companies that invest in sustainability, automation, and workforce training will be best positioned to compete in the evolving global market. While large-scale employment recovery is unlikely, the paper industry will continue to play a vital role in the American economy as a key supplier of packaging, hygiene, and specialty paper products.
Printing and Related Support Activities (NAICS 323)
The Printing and Related Support Activities subsector has long been a staple of American manufacturing, encompassing a wide range of services, including commercial printing, book publishing, and digital printing. However, employment in the industry has declined significantly over the past three decades due to technological advancements, shifts in consumer behavior, and competition from digital media.
Employment Trends
Employment in Printing and Related Support Activities has seen a steady decline since 1990, when the industry employed over 800,000 workers. By 2024, employment had fallen to approximately 400,000, marking a 50% decrease over three decades.

Several key factors have contributed to this decline:
- The rise of digital media and online advertising has reduced demand for printed materials such as newspapers, magazines, and directories.
- Automation and digital printing technologies have increased efficiency but reduced the need for manual labor.
- Outsourcing of print production to overseas facilities has further impacted employment in the U.S.
- Decline in physical book printing, with the shift toward e-books and online content.
Despite these challenges, certain segments of the industry—such as packaging, specialty printing, and labels—have remained resilient due to ongoing demand.
Industry Composition
The Printing and Related Support Activities sector is divided into three primary categories:
- Commercial Printing (NAICS 32311)
- Involves the production of books, brochures, magazines, business forms, and marketing materials.
- Has seen a dramatic decline due to digitization and the decline of traditional print media.
- Support Activities for Printing (NAICS 32312)
- Includes prepress services such as plate-making, typesetting, and binding.
- Has been impacted by automation and digital workflow technologies, reducing employment in traditional roles.
- Specialized and Niche Printing (Custom Printing, Packaging, and Labels)
- Growth areas include flexographic and digital label printing, packaging materials, and customized print-on-demand services.
- Demand for sustainable and biodegradable packaging has driven investment in this sector.
Technology and Automation in Printing
Printing has been one of the most heavily automated sectors within manufacturing, driven by innovations in digital printing, offset printing, and prepress automation. Key advancements include:
- Computer-to-plate (CTP) technology, eliminating traditional film-based plate-making.
- Digital printing systems, allowing faster, cost-effective, and on-demand production.
- AI-driven workflow automation, reducing the need for manual layout and prepress workers.
- 3D printing and specialty graphics printing, opening new markets for the industry.
While these technologies have improved efficiency and lowered costs, they have also led to significant job losses in traditional printing operations.
Workforce Challenges
The industry faces several key workforce challenges, including:
- A shrinking talent pool: As the industry contracts, fewer workers are entering the field, making it difficult to fill specialized roles.
- Technical skills gap: Modern printing requires expertise in digital workflows, press operation, and color management.
- Aging workforce: Many experienced print operators are retiring, and younger workers are not replacing them at the same rate.
To address these challenges, apprenticeship programs and vocational training initiatives are being expanded to help workers transition into digital printing, prepress automation, and specialty printing roles.
Geographic Distribution
Printing industry jobs are concentrated in key metropolitan areas with large publishing, advertising, and packaging hubs, including:
- Illinois (Chicago area) – A major hub for commercial printing and packaging.
- California (Los Angeles and San Francisco) – Strong in digital printing, specialty graphics, and label production.
- New York (New York City area) – Focus on publishing, marketing materials, and high-end custom printing.
- Pennsylvania and Ohio – Home to large-scale packaging and flexographic printing operations.
Future Outlook
While traditional printing continues to decline, several emerging trends and markets may stabilize or even grow portions of the industry:
- Growth in Packaging and Label Printing
- E-commerce growth has increased demand for custom packaging and labels.
- Sustainable and eco-friendly packaging solutions are driving investment in biodegradable printing materials.
- Digital and On-Demand Printing
- Print-on-demand services for books, marketing materials, and personalized products are expanding.
- Variable data printing (VDP) allows mass customization, creating opportunities in targeted marketing.
- 3D Printing and Advanced Graphics
- 3D printing is opening new applications in industrial prototyping, medical devices, and high-tech manufacturing.
- Growth in specialty printing (e.g., textiles, direct-to-object printing) could create new job opportunities.
- Sustainability Initiatives
- Soy-based inks, recycled paper, and waterless printing are gaining traction as environmental concerns reshape the industry.
- Government regulations on single-use plastics may push companies toward paper-based alternatives.
- Reshoring of High-End Printing
- Rising labor costs overseas and concerns over supply chain resilience may lead to the reshoring of high-value print production.
The Printing and Related Support Activities sector has undergone massive changes, with employment cut in half since 1990 due to digitization, automation, and outsourcing. While traditional printing jobs continue to decline, growth areas like packaging, digital printing, and sustainable solutions are creating new opportunities.
Moving forward, investment in workforce training, digital innovation, and eco-friendly printing technologies will be critical in preserving jobs and keeping the sector competitive. While the industry is unlikely to return to its previous employment levels, it remains a crucial part of American manufacturing, particularly in packaging, specialty graphics, and on-demand printing.
Petroleum and Coal Products Manufacturing (NAICS 324)
The petroleum and coal products manufacturing sector is a critical part of the U.S. industrial economy, producing refined petroleum, asphalt, lubricants, and coal-based products. This subsector plays an essential role in energy production, infrastructure, and transportation. Despite its importance, employment in this industry has seen long-term declines due to automation, shifting energy policies, and fluctuating oil markets.
Employment Trends
Employment in petroleum and coal products manufacturing has steadily declined over the past three decades. In 1990, the sector employed approximately 150,000 workers. By 2024, that number had dropped to around 110,000, reflecting a 27% decrease over the period.
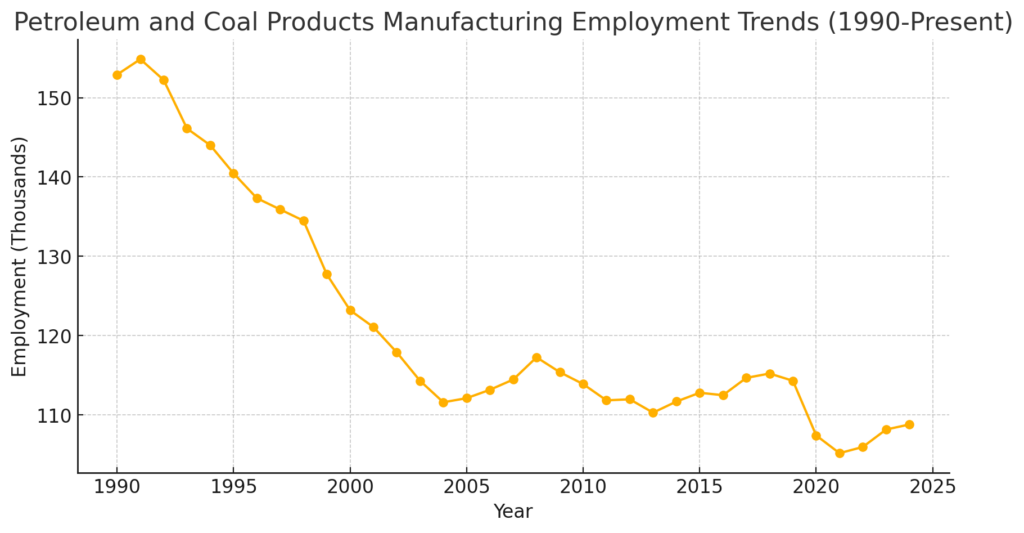
Several key factors have contributed to this decline:
- Automation and process efficiency: Modern refining and processing plants require fewer workers due to the increased use of automated systems.
- Declining domestic coal demand: The U.S. coal industry has contracted sharply as power plants transition to natural gas and renewable energy.
- Energy market volatility: Global oil price fluctuations and policy shifts impact refinery employment and production capacity.
- Regulatory and environmental pressures: Stricter emissions regulations and carbon reduction targets have led to plant closures and restructuring.
While overall employment has declined, certain segments within the industry, such as specialty petroleum products and advanced refining technologies, have seen stable or growing employment levels.
Industry Composition
The petroleum and coal products manufacturing sector consists of two primary industries:
- Petroleum Refining (NAICS 324110)
- Includes crude oil refining to produce gasoline, diesel, jet fuel, and petrochemicals.
- Dominated by large multinational corporations operating massive refining complexes.
- Heavily influenced by energy prices and environmental regulations.
- Coal Products and Asphalt Manufacturing (NAICS 324121 & NAICS 324122)
- Produces asphalt paving materials, roofing products, and industrial coal-derived products.
- Employment has declined due to lower demand for coal-based products and a shift toward alternative materials.
Technology and Automation in Petroleum and Coal Manufacturing
The industry has embraced automation and digital transformation, leading to significant efficiency gains but reducing the need for traditional labor.
- Advanced process control systems allow refineries to optimize operations with fewer human operators.
- AI and machine learning are used for predictive maintenance, reducing unplanned downtime and labor needs.
- Hydrocracking and biofuel conversion technologies are expanding as refineries adapt to evolving fuel regulations.
- Digital twins and real-time monitoring improve refinery safety and efficiency, reducing manual intervention.
While these technologies have streamlined operations, they have also led to a decline in traditional refining and coal-processing jobs, requiring a workforce with advanced technical skills.
Workforce Challenges
Despite technological advancements, the industry faces several workforce challenges:
- Aging workforce: Many experienced refinery and processing plant workers are nearing retirement, and there are fewer younger workers entering the industry.
- Shifts in required skill sets: The rise of digital and automated systems has increased demand for engineers, data analysts, and technicians with specialized training.
- Regulatory uncertainty: Environmental regulations and evolving energy policies create instability, making long-term workforce planning difficult.
- Geographic concentration of jobs: Refineries and processing plants are concentrated in specific regions, limiting job opportunities for displaced workers in other areas.
To address these challenges, companies are investing in workforce training, apprenticeship programs, and partnerships with technical schools to attract and retain skilled workers.
Geographic Distribution
The petroleum and coal products manufacturing sector is heavily concentrated in key refining and coal-processing hubs:
- Texas (Houston, Corpus Christi, Port Arthur) – The leading state in petroleum refining, home to some of the largest refineries in the world.
- Louisiana (Baton Rouge, New Orleans) – Major refining and petrochemical manufacturing center.
- California (Los Angeles, Bay Area) – Houses several large refineries but faces increasing regulatory pressures.
- Pennsylvania and West Virginia – Historically strong in coal production, though employment has declined sharply.
- Midwest and Gulf Coast states – Play significant roles in asphalt production and specialty petroleum processing.
Future Outlook
While traditional refining employment is expected to decline further, several trends could stabilize or reshape the industry:
- Growth of Alternative Fuels and Biofuels
- Federal and state policies promoting low-carbon fuels could drive investment in bio-refineries.
- Companies are increasingly producing renewable diesel, ethanol, and hydrogen-based fuels.
- Carbon Capture and Sustainability Investments
- Refineries are investing in carbon capture and storage (CCS) technologies to comply with emissions regulations.
- The shift toward net-zero commitments could create new jobs in emissions reduction projects.
- Expansion of Petrochemicals and Specialty Products
- The demand for plastics, synthetic lubricants, and industrial chemicals remains strong.
- Growth in battery materials production (e.g., lithium refining for EVs) could provide new employment opportunities.
- Reshoring of Strategic Energy Production
- Geopolitical concerns and supply chain disruptions are leading to renewed interest in domestic energy independence.
- Policy shifts could encourage investment in U.S.-based refining and fuel production.
- Declining Coal Industry, but Potential for Repurposing
- While traditional coal product employment continues to shrink, some facilities are exploring conversion to alternative fuel processing.
- Government funding for coal-to-clean-energy transitions could lead to new industrial jobs in former coal regions.
The petroleum and coal products manufacturing sector remains a critical component of the U.S. economy, but its employment landscape is shifting due to automation, energy policy changes, and the global transition toward lower-carbon energy sources.
While overall employment is unlikely to return to previous levels, investments in biofuels, carbon capture, and petrochemical innovations could create new opportunities in the sector. Companies and policymakers must focus on workforce retraining, sustainability initiatives, and technological adaptation to ensure the industry remains competitive in the evolving energy landscape.
Chemical Manufacturing (NAICS 325)
The chemical manufacturing sector is one of the largest and most diverse industries in U.S. manufacturing, producing essential materials for pharmaceuticals, agriculture, construction, and consumer goods. It plays a vital role in the economy, contributing significantly to exports, innovation, and high-wage employment.
Employment Trends
Employment in chemical manufacturing has remained relatively stable compared to other manufacturing sectors, but it has still seen gradual declines due to automation and industry consolidation. In 1990, the sector employed over 1 million workers. By 2024, employment stood at approximately 800,000, representing a 20% decline over three decades. But, this subsector has seen a significant rise in employment since 2011.
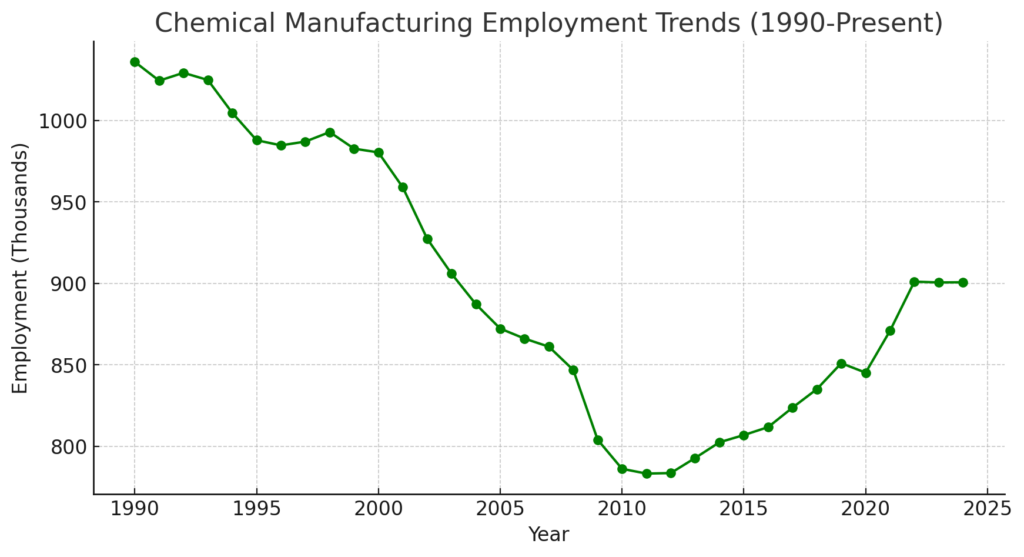
Several key factors have shaped employment trends in this industry:
- Automation and efficiency improvements: Advanced production processes have increased output while reducing the need for manual labor.
- Industry consolidation: Mergers and acquisitions have streamlined operations, leading to workforce reductions.
- Global competition: The offshoring of chemical production, particularly in pharmaceuticals and basic chemicals, has impacted domestic employment.
- Regulatory challenges: Environmental regulations have influenced investment decisions, particularly in specialty chemicals and petrochemicals.
Despite these challenges, the industry remains a high-wage employer with strong job opportunities in specialized fields such as biotechnology, pharmaceuticals, and advanced materials.
Industry Composition
The chemical manufacturing sector is divided into several major subsectors, each with unique characteristics and workforce demands:
- Basic Chemical Manufacturing (NAICS 3251)
- Produces bulk chemicals such as acids, industrial gases, and petrochemicals.
- Faces global competition but benefits from U.S. natural gas production for feedstocks.
- Resin, Synthetic Rubber, and Artificial Fibers (NAICS 3252)
- Supplies plastics, synthetic fibers, and rubber products to multiple industries.
- Has grown due to increased demand for lightweight materials in automotive and aerospace manufacturing.
- Pharmaceutical and Medicine Manufacturing (NAICS 3254)
- One of the fastest-growing segments, driven by drug development and medical advancements.
- Faces increasing reshoring efforts due to supply chain vulnerabilities exposed by the COVID-19 pandemic.
- Paint, Coating, and Adhesive Manufacturing (NAICS 3255)
- Supplies coatings for construction, automotive, and consumer goods industries.
- Faces regulatory scrutiny due to volatile organic compound (VOC) emissions.
- Soap, Cleaning Compound, and Toilet Preparation Manufacturing (NAICS 3256)
- Includes personal care products, detergents, and industrial cleaners.
- Growth driven by hygiene trends and increasing demand for eco-friendly products.
- Other Chemical Product and Preparation Manufacturing (NAICS 3259)
- Produces specialized chemicals such as explosives, photographic chemicals, and custom compounds.
- Niche but critical for industries like defense and advanced manufacturing.
Technology and Automation in Chemical Manufacturing
The chemical manufacturing sector has long been at the forefront of industrial automation. Modern facilities integrate advanced technologies to improve efficiency, safety, and product quality. Key advancements include:
- AI-driven process control: Uses machine learning to optimize production in real-time.
- Advanced robotics: Reduces the need for manual labor in hazardous environments.
- 3D printing of chemicals: Emerging applications for producing complex molecules and materials.
- Sustainable chemistry innovations: Green chemistry principles are being applied to reduce waste and energy consumption.
While these innovations enhance productivity, they also reduce employment in traditional production roles, requiring a shift toward more technical and engineering-based jobs.
Workforce Challenges
Despite its high-tech nature, the chemical industry faces several workforce challenges:
- Aging workforce: Many experienced chemical plant operators and engineers are nearing retirement, creating a talent gap.
- Need for specialized training: The shift toward automated production requires workers with skills in programming, data analytics, and process control.
- Regulatory compliance expertise: Workers must navigate complex environmental and safety regulations, increasing the demand for compliance specialists.
- Reshoring and supply chain changes: Government policies encouraging domestic production of critical chemicals, especially pharmaceuticals, could create workforce shortages if training pipelines are not expanded.
Geographic Distribution
Chemical manufacturing employment is concentrated in key industrial regions:
- Texas and Louisiana – Home to the largest petrochemical and refinery complexes, benefiting from Gulf Coast shipping and natural gas resources.
- Midwest (Illinois, Ohio, Michigan) – Strong presence in coatings, adhesives, and industrial chemicals.
- Northeast (New Jersey, Pennsylvania, Massachusetts) – A major hub for pharmaceutical manufacturing.
- California – Leading producer of specialty chemicals, particularly in biotechnology and consumer products.
Future Outlook
While overall employment is unlikely to return to peak levels, several trends could drive growth in specific segments:
- Expansion of the pharmaceutical industry
- Efforts to reshore drug manufacturing could lead to increased investment in domestic production facilities.
- Growth in biologics, gene therapies, and personalized medicine may create new job opportunities.
- Green chemistry and sustainability
- Regulatory and consumer demand for eco-friendly chemicals is pushing innovation.
- Biodegradable plastics, non-toxic coatings, and renewable chemical processes are becoming industry priorities.
- Advanced materials and nanotechnology
- Increasing demand for lightweight composites, high-performance polymers, and energy-efficient coatings could fuel job growth.
- Nanomaterials are being explored for use in electronics, medical devices, and energy storage.
- Reshoring and national security concerns
- The U.S. government is incentivizing domestic production of critical materials, reducing reliance on China and other foreign suppliers.
- Defense and high-tech industries are investing in strategic chemical supply chains.
- Workforce development initiatives
- Companies are partnering with universities and technical schools to address skill shortages.
- Apprenticeship programs and STEM education initiatives are expanding to prepare the next generation of chemical workers.
Chemical manufacturing remains one of the most resilient and high-paying sectors in U.S. manufacturing, despite gradual declines in overall employment. While traditional production jobs have decreased due to automation and consolidation, emerging opportunities in pharmaceuticals, green chemistry, and advanced materials offer new pathways for job growth.
The industry must continue to adapt to sustainability demands, regulatory pressures, and workforce shortages to maintain its global competitiveness. Investment in innovation, workforce training, and supply chain resilience will be key factors in shaping the future of chemical manufacturing in the United States.
Plastics and Rubber Products Manufacturing (NAICS 326)
The Plastics and Rubber Products Manufacturing sector plays a crucial role in the U.S. economy, supplying essential materials to industries such as automotive, construction, healthcare, and consumer goods. Over the past three decades, employment in this sector has experienced fluctuations, with a significant decline in the early 2000s followed by a notable resurgence in the last 15 years.
Employment Trends
Employment in Plastics and Rubber Products Manufacturing peaked in the late 1990s before experiencing a steep decline in the early 2000s due to offshoring, automation, and economic downturns. However, in contrast to many other manufacturing sectors, employment in this industry has shown signs of stabilization and growth since around 2010.
- In 1990, the sector employed approximately 820,000 workers.
- During the early 2000s, employment dropped significantly due to globalization and industry consolidation, falling below 800,000.
- By 2010, employment had stabilized at around 750,000.
- Since 2010, the sector has experienced steady job growth, reaching around 900,000 workers in 2024.
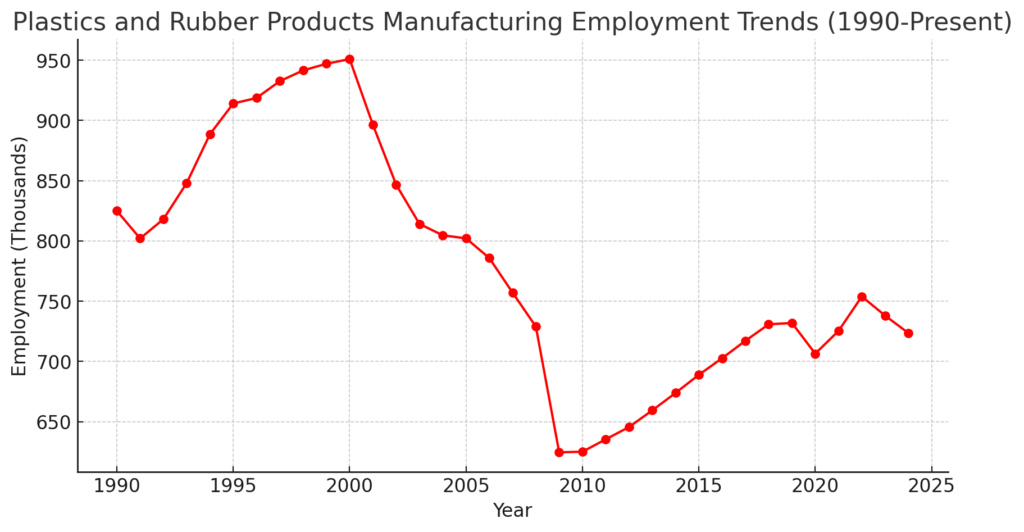
This 15-year resurgence can be attributed to several factors:
- The reshoring of plastic manufacturing due to supply chain concerns and increasing costs of overseas production.
- Booming demand for plastic-based packaging and medical supplies, especially following the COVID-19 pandemic.
- Growth in advanced polymer and composite materials, used in industries such as aerospace and electric vehicles.
- Automation enabling cost-effective domestic production, making U.S. manufacturers more competitive.
Industry Composition
The Plastics and Rubber Products Manufacturing sector consists of two primary industries:
- Plastics Product Manufacturing (NAICS 3261)
- The largest segment, producing a wide range of plastic goods, including packaging, containers, pipes, and automotive components.
- Has seen consistent growth due to the rising demand for lightweight, durable materials.
- Rubber Product Manufacturing (NAICS 3262)
- Includes tire manufacturing, rubber hoses, belts, and industrial rubber products.
- More volatile due to its reliance on the automotive industry but benefiting from the growth of electric vehicles (EVs).
Technology and Automation in Plastics and Rubber Manufacturing
The sector has increasingly adopted automation and advanced materials science to improve efficiency, reduce costs, and enhance product performance. Some key technological advancements include:
- Injection molding and robotic automation, reducing production costs while maintaining quality.
- 3D printing with plastics, allowing for rapid prototyping and small-batch production.
- Biodegradable and recycled plastics, responding to environmental concerns and consumer demand.
- Smart polymers and self-healing materials, driving innovation in medical and industrial applications.
While automation has replaced some traditional labor-intensive jobs, the rise of specialized and high-tech plastic materials has created new job opportunities in research, engineering, and production.
Workforce Challenges
Despite recent growth, the Plastics and Rubber Products Manufacturing industry faces key workforce challenges:
- A shortage of skilled workers in advanced manufacturing roles, including machine operators and process engineers.
- Public perception issues, as plastics face increased scrutiny due to environmental concerns.
- Shifts in regulatory policies, including potential bans on single-use plastics, requiring adaptation and innovation in sustainable materials.
- Global competition, particularly from China and Southeast Asia, which continues to produce low-cost plastic goods.
Geographic Distribution
Plastics and rubber manufacturing employment is concentrated in states with strong industrial and automotive sectors:
- Ohio, Indiana, and Michigan – Home to major auto suppliers and plastic molding facilities.
- Texas and Louisiana – Leading producers of plastic resins and raw materials, benefiting from Gulf Coast petrochemical production.
- California – A key center for consumer goods manufacturing and high-tech plastic innovations.
- Illinois and Wisconsin – Major hubs for packaging, medical plastics, and industrial rubber products.
Future Outlook
While traditional plastic manufacturing faces increasing regulatory pressure, several trends are driving new opportunities in the sector:
- Growth in Sustainable and Biodegradable Plastics
- The demand for eco-friendly alternatives to traditional plastics is rising.
- Investments in recyclable and compostable materials could create jobs in next-generation plastics production.
- Advancements in High-Performance Polymers
- Growth in aerospace, medical devices, and EVs is driving demand for stronger, lighter plastic composites.
- Thermoplastics and carbon fiber-reinforced polymers are expected to expand the industry.
- Automation and Smart Manufacturing
- AI-driven process optimization and robotic automation are making U.S. plastic production more competitive.
- 3D printing in plastics is growing, enabling localized production and reducing reliance on overseas suppliers.
- Reshoring and Supply Chain Resilience
- The COVID-19 pandemic exposed vulnerabilities in global supply chains, leading to increased investment in domestic plastic and rubber production.
- Companies are reducing dependence on China and other foreign suppliers, creating new job opportunities in the U.S.
- Expansion of Electric Vehicles (EVs)
- The transition to EVs requires lighter, high-performance plastic materials to replace metal components.
- Rubber and tire production is shifting to accommodate new EV-specific designs and sustainable rubber alternatives.
The Plastics and Rubber Products Manufacturing sector has undergone significant shifts over the past 30 years, with a major decline in the early 2000s followed by a surprising resurgence over the last 15 years. The industry remains critical to U.S. manufacturing, supporting key sectors such as automotive, healthcare, consumer goods, and packaging.
Looking ahead, innovation in sustainable materials, automation, and reshoring efforts will shape the industry’s future. While challenges such as environmental regulations and global competition persist, investment in workforce training and next-generation plastics technology will be key to maintaining the sector’s momentum.
Nonmetallic Mineral Product Manufacturing (NAICS 327)
The nonmetallic mineral product manufacturing sector produces essential materials for construction, infrastructure, and industrial applications. This includes cement, glass, ceramics, and other materials used in residential, commercial, and public works projects.
Employment Trends
Employment in nonmetallic mineral product manufacturing has experienced long-term fluctuations, peaking in the late 1970s before declining due to automation and global competition. However, since 2011, the sector has shown signs of resurgence, driven by increased construction activity, infrastructure investment, and a shift toward sustainable building materials.
- In 1951, the sector employed around 530,000 workers.
- Employment peaked in the late 1970s, surpassing 600,000.
- A long-term decline followed, with employment dropping below 500,000 by the early 2000s.
- The 2008 financial crisis hit the industry hard, with employment falling sharply.
- Since 2011, the sector has experienced steady growth, reaching approximately 400,000 workers in 2024.
This recovery is linked to increased infrastructure spending, a rebound in housing construction, and advances in green building materials.
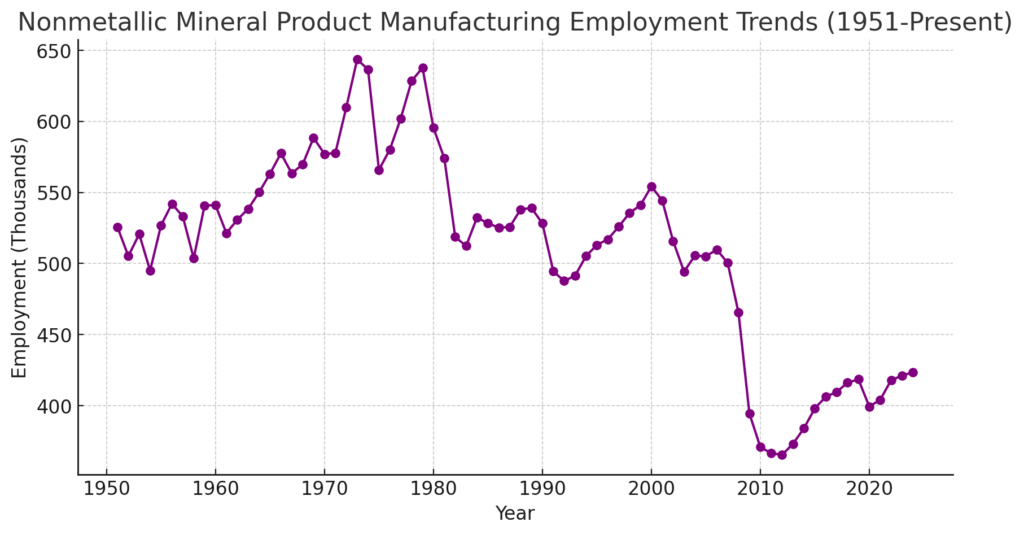
Industry Composition
The nonmetallic mineral product manufacturing sector consists of several key industries:
- Cement and Concrete Product Manufacturing (NAICS 3273)
- The largest segment, supplying materials for roads, bridges, and buildings.
- Demand has surged due to government infrastructure projects.
- Glass and Glass Product Manufacturing (NAICS 3272)
- Produces glass for windows, vehicles, electronics, and solar panels.
- Growth in renewable energy has increased demand for high-performance glass.
- Clay Product and Refractory Manufacturing (NAICS 3271)
- Includes bricks, ceramics, and heat-resistant materials for industrial use.
- The rise in domestic manufacturing has led to renewed demand for refractories.
- Other Nonmetallic Mineral Product Manufacturing (NAICS 3279)
- Includes gypsum, lime, and mineral-based insulation.
- Increasing focus on energy-efficient materials has driven innovation in this category.
Technology and Automation in Nonmetallic Mineral Manufacturing
The sector has adopted automation to improve efficiency and reduce costs. Some of the most significant technological advancements include:
- AI and machine learning in cement mixing and quality control.
- Automated glass cutting and shaping for construction and automotive applications.
- 3D printing with cement-based materials, used in prefabricated construction.
- Development of energy-efficient kilns and low-carbon cement to reduce emissions.
While automation has reduced the need for manual labor, it has also created demand for skilled workers who can operate and maintain these technologies.
Workforce Challenges
Despite recent growth, the industry faces several workforce challenges:
- A shortage of skilled tradespeople, particularly in cement and glass manufacturing.
- The need for training programs to support automation and digital manufacturing.
- High energy costs and environmental regulations that impact production methods.
- The impact of construction cycles on employment stability.
To address these issues, industry leaders are investing in apprenticeship programs and partnerships with vocational schools.
Geographic Distribution
Employment in nonmetallic mineral manufacturing is concentrated in states with strong construction and infrastructure sectors:
- Texas and California – Major hubs for cement, concrete, and glass production.
- Pennsylvania and Ohio – Strong in clay products and mineral-based manufacturing.
- Florida and the Southeast – High demand for construction materials due to population growth.
- Midwest and Great Plains – Significant cement production for public infrastructure projects.
Future Outlook
Several factors are expected to shape the industry’s future:
- Growth in Infrastructure Investment
- Federal spending on roads, bridges, and public transit will drive demand for cement and concrete products.
- Expansion of Renewable Energy
- The rise of solar and wind power will boost demand for advanced glass and insulation materials.
- Sustainable and Low-Carbon Materials
- Research into carbon-neutral cement and energy-efficient glass is gaining momentum.
- Automation and Digital Manufacturing
- The use of smart factories and AI-driven production processes will reshape the workforce.
- Reshoring of Construction Materials
- Supply chain disruptions have led to renewed interest in domestic production of essential building materials.
Nonmetallic mineral product manufacturing remains a foundational industry for U.S. infrastructure and construction. While employment has fluctuated over the decades, the sector has shown resilience, with a strong recovery since 2011. Continued investment in infrastructure, sustainability, and automation will play a key role in shaping the industry’s future.
Primary Metal Manufacturing (NAICS 331)
The primary metal manufacturing sector is a cornerstone of American industry, producing raw metal materials used in construction, automotive, aerospace, and machinery manufacturing. This sector includes the production of steel, aluminum, and other non-ferrous metals, which serve as essential inputs for countless downstream industries.
Employment Trends
Employment in primary metal manufacturing has declined significantly over the past three decades, largely due to globalization, automation, and shifts in domestic demand. However, there have been periods of stabilization and resurgence in recent years, especially due to reshoring efforts and increased investment in domestic steel and aluminum production.
- In 1990, the sector employed approximately 688,000 workers.
- Employment steadily declined through the 1990s and early 2000s due to foreign competition and industry consolidation.
- The Great Recession (2007–2009) led to a sharp decline, with employment falling below 400,000.
- Since 2010, the sector has seen stabilization, with employment hovering around 350,000 to 400,000 workers.
- Recent policy shifts, including tariffs on foreign steel and aluminum, have helped sustain employment levels.
The industry’s future will be shaped by government policies, global trade conditions, and the shift toward advanced metal alloys and sustainable production practices.
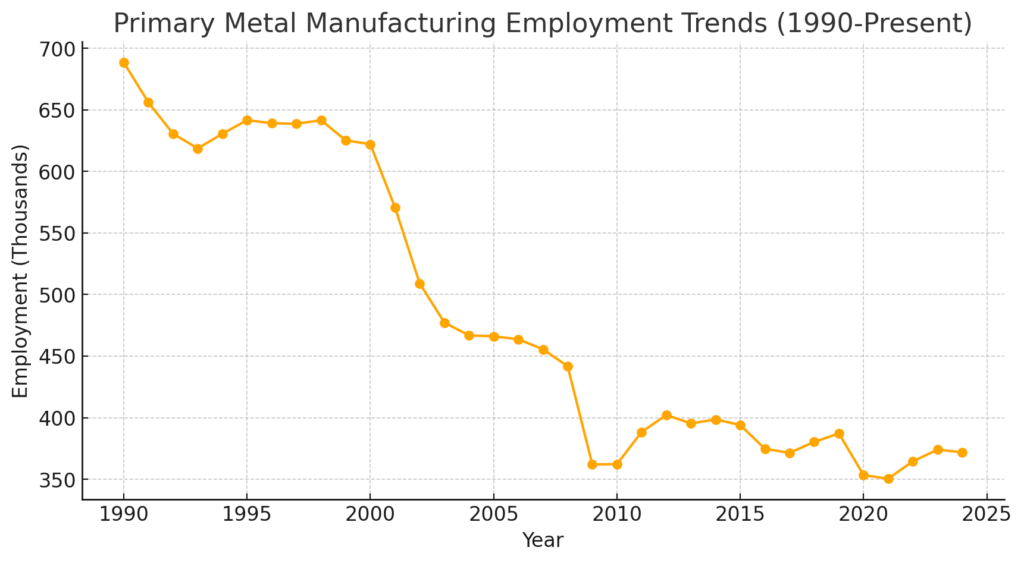
Industry Composition
The primary metal manufacturing sector consists of several major industries:
- Iron and Steel Mills and Ferroalloy Manufacturing (NAICS 3311)
- Produces crude iron, steel, and ferroalloys used in construction, machinery, and transportation.
- Heavily impacted by global steel prices and trade policies.
- Alumina and Aluminum Production (NAICS 3313)
- Produces aluminum sheets, plates, and extrusions for aerospace, automotive, and packaging industries.
- Increasing demand due to the rise of electric vehicles (EVs) and lightweight materials.
- Nonferrous Metal Production (NAICS 3314)
- Includes copper, nickel, and specialty alloys used in electronics and energy applications.
- Growing demand for copper and rare metals due to renewable energy projects.
- Foundries (NAICS 3315)
- Produces metal castings used in industrial machinery and transportation.
- Facing workforce shortages due to the technical nature of foundry work.
Technology and Automation in Primary Metal Manufacturing
The industry has undergone major technological advancements to increase efficiency and reduce environmental impact. Some of the most significant developments include:
- Electric arc furnaces (EAFs), which have largely replaced traditional blast furnaces, reducing emissions and increasing efficiency.
- AI-driven process optimization, allowing mills to maximize yields and minimize waste.
- Hydrogen-based steel production, an emerging technology that could significantly cut carbon emissions.
- Advanced metal recycling, helping reduce reliance on newly mined raw materials.
These advancements have reduced the need for manual labor while increasing demand for highly skilled workers in metallurgy, automation, and robotics.
Workforce Challenges
Despite recent stabilization in employment, the sector faces several long-term challenges:
- Aging workforce: Many skilled metalworkers are nearing retirement, and there is a shortage of younger workers entering the industry.
- Trade policy uncertainty: Tariffs on foreign steel and aluminum have provided temporary relief, but global competition remains intense.
- Energy costs: Metal production is energy-intensive, and fluctuations in electricity and raw material costs impact profitability.
- Environmental regulations: Stricter emissions rules are forcing companies to adopt cleaner production methods, requiring retraining for workers.
To address these issues, industry groups are investing in workforce development programs, vocational training, and partnerships with community colleges.
Geographic Distribution
Primary metal manufacturing is concentrated in regions with strong industrial and transportation infrastructure:
- Midwest (Ohio, Indiana, Illinois, Pennsylvania, Michigan) – Historically the heart of U.S. steel production, with major mills and foundries.
- South (Texas, Alabama, Kentucky, Tennessee) – Emerging as a hub for aluminum and specialty metal production.
- West Coast (California, Washington, Oregon) – Home to aluminum producers and aerospace-related metal suppliers.
Future Outlook
Several key trends are expected to influence the sector’s future:
- Growth in Sustainable Metal Production
- The rise of green steel and low-carbon aluminum is creating opportunities for new investment.
- Hydrogen-based smelting and carbon capture technologies could reshape the industry.
- Demand for Lightweight Metals in Transportation
- The automotive and aerospace industries are shifting toward lightweight aluminum and titanium alloys.
- The expansion of electric vehicles (EVs) is increasing the need for advanced aluminum production.
- Reshoring and Supply Chain Resilience
- The COVID-19 pandemic exposed vulnerabilities in global supply chains, leading to increased investment in domestic metal production.
- Government incentives for U.S.-based steel and aluminum production could help sustain employment.
- Advanced Recycling and Circular Economy
- Growing emphasis on metal recycling and reuse could reduce dependence on mining and lower production costs.
- Investments in urban mining and scrap metal processing are gaining traction.
- Workforce Development and Automation
- The need for skilled metallurgists, machine operators, and automation specialists will continue to grow.
- Training programs are being expanded to address the skills gap in modern metal production.
Primary metal manufacturing remains a critical sector for U.S. industry, providing essential materials for construction, transportation, and high-tech applications. While employment has declined from historical levels, recent stabilization and growth in advanced metal production suggest a more resilient future. Investments in sustainable production methods, automation, and workforce development will determine the sector’s long-term competitiveness.
Fabricated Metal Product Manufacturing (NAICS 332)
The fabricated metal product manufacturing sector plays a crucial role in the U.S. economy, producing essential components for industries such as construction, automotive, aerospace, and industrial machinery. This sector includes the manufacturing of structural metal products, machine parts, fasteners, and a wide range of precision-engineered components.
Employment Trends
Employment in fabricated metal product manufacturing has experienced long-term fluctuations, with a notable decline in the early 2000s followed by partial recovery in recent years.
- In 1990, the sector employed approximately 1.7 million workers.
- Employment declined significantly between 2000 and 2010 due to offshoring, automation, and economic downturns.
- The Great Recession (2007–2009) led to a sharp drop, with employment bottoming out at around 1.2 million in 2010.
- Since 2011, employment has shown steady recovery, reaching approximately 1.4 million workers in 2024.
The recent stabilization is linked to the reshoring of metal fabrication jobs, rising demand for domestic manufacturing, and increased investment in advanced production technologies.
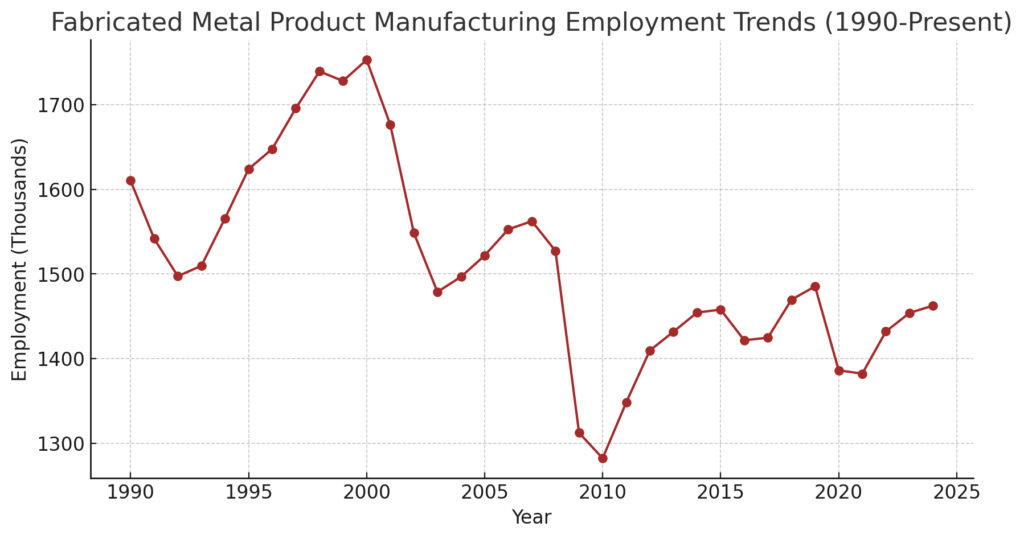
Industry Composition
The fabricated metal product manufacturing sector consists of several major industries:
- Architectural and Structural Metals Manufacturing (NAICS 3323)
- Produces metal frames, doors, and bridges for construction projects.
- Demand is growing due to infrastructure investment.
- Machine Shops and Threaded Products Manufacturing (NAICS 3327)
- Includes machining of custom metal components and precision engineering.
- Benefiting from growth in aerospace and high-tech industries.
- Coating, Engraving, Heat Treating, and Allied Activities (NAICS 3328)
- Focuses on metal finishing and surface treatments for durability and performance.
- Increasing demand from defense and electronics manufacturers.
- Other Fabricated Metal Product Manufacturing (NAICS 3329)
- Includes fasteners, cutlery, and small metal products used in industrial applications.
- Steady growth due to automation and robotics integration.
Technology and Automation in Fabricated Metal Manufacturing
The sector has increasingly adopted advanced manufacturing technologies to enhance efficiency, quality, and cost-effectiveness. Some of the most impactful innovations include:
- Computer numerical control (CNC) machining for high-precision parts.
- Laser cutting and robotic welding for structural metal components.
- Additive manufacturing (metal 3D printing) for aerospace and medical applications.
- AI-driven quality control systems to reduce defects and waste.
While automation has reduced labor-intensive jobs, it has also created new opportunities for skilled workers specializing in programming, machine operation, and maintenance of advanced systems.
Workforce Challenges
Despite employment gains in recent years, the industry faces several workforce challenges:
- A shortage of skilled machinists, welders, and metal fabricators.
- The need for retraining workers as automation replaces traditional roles.
- Rising raw material costs affecting profitability and job stability.
- Trade policy uncertainty, particularly regarding steel and aluminum tariffs.
To address these challenges, manufacturers are investing in apprenticeship programs, technical education partnerships, and upskilling initiatives.
Geographic Distribution
Fabricated metal manufacturing employment is concentrated in states with strong industrial bases:
- Midwest (Illinois, Ohio, Indiana, Michigan, Wisconsin) – A historic hub for metal fabrication and industrial machinery.
- Texas and the Southeast (Alabama, Georgia, Tennessee, Kentucky) – Growing manufacturing centers for aerospace, automotive, and structural metals.
- California and the West Coast – Home to precision metal manufacturing for technology, aerospace, and defense industries.
Future Outlook
Several trends are expected to shape the future of fabricated metal manufacturing:
- Growth in Infrastructure and Construction
- Increased federal investment in bridges, roads, and commercial buildings will sustain demand for structural metal components.
- Advanced Manufacturing and Automation
- Smart factories integrating AI, robotics, and real-time monitoring will enhance efficiency and create higher-skilled job opportunities.
- Reshoring and Supply Chain Resilience
- Companies are reducing reliance on overseas suppliers, bringing production back to the U.S. to avoid supply chain disruptions.
- Expansion of Electric Vehicles and Renewable Energy
- Fabricated metal products are essential for EV battery enclosures, wind turbine structures, and solar panel mounting systems.
- Sustainability and Green Manufacturing
- The industry is adopting energy-efficient processes and increasing the use of recycled metals to reduce environmental impact.
Fabricated metal product manufacturing remains a critical sector in U.S. manufacturing, supporting infrastructure, transportation, and industrial machinery. While employment has declined from historical peaks, recent stabilization and technological advancements suggest a more competitive future. Investment in workforce training, automation, and domestic supply chains will be key to sustaining long-term growth.
Machinery Manufacturing (NAICS 333)
The machinery manufacturing sector is a key component of U.S. manufacturing, producing industrial equipment, construction machinery, agricultural machines, and other specialized products that support multiple industries, including energy, transportation, and defense. This sector is highly technology-driven, with increasing automation and integration of smart manufacturing systems.
Employment Trends
Employment in machinery manufacturing has fluctuated significantly over the past few decades, with a decline in the early 2000s followed by a period of stability and modest recovery in recent years.
- In 1990, the sector employed approximately 1.4 million workers.
- Employment declined steadily between 2000 and 2010, largely due to offshoring and automation.
- The Great Recession (2007–2009) led to further job losses, with employment bottoming out at around 950,000 in 2010.
- Since 2011, the sector has experienced gradual recovery, reaching around 1.1 million workers in 2024.
This stabilization can be attributed to reshoring efforts, the demand for high-tech industrial equipment, and increased automation requiring skilled labor.
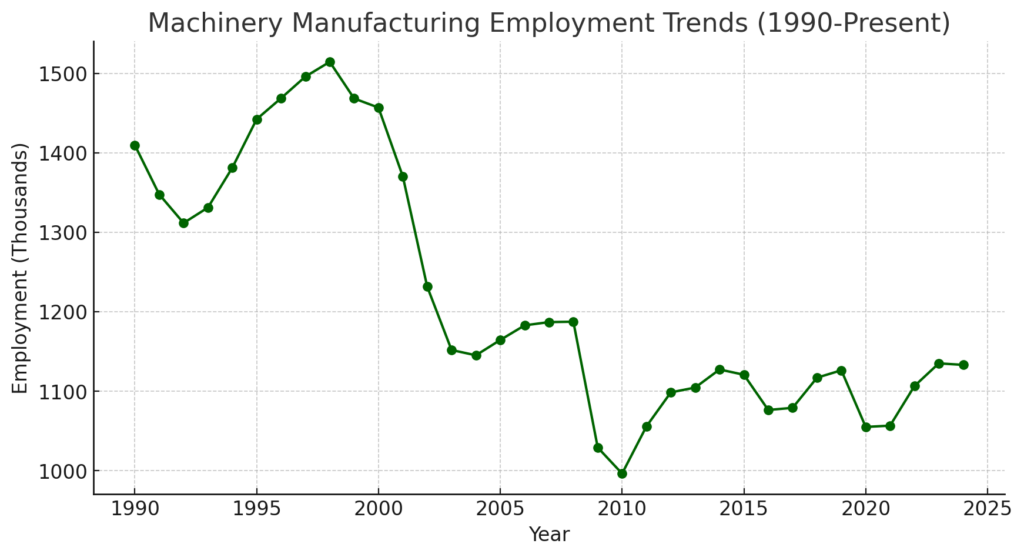
Industry Composition
The machinery manufacturing sector consists of several major industries:
- Agricultural, Construction, and Mining Machinery Manufacturing (NAICS 3331)
- Includes tractors, excavators, mining equipment, and related heavy machinery.
- Growth has been driven by infrastructure investment and modernization in farming.
- Industrial Machinery Manufacturing (NAICS 3332)
- Produces equipment used in manufacturing processes, including robotics and automation systems.
- Benefiting from increased automation in domestic manufacturing.
- Commercial and Service Industry Machinery Manufacturing (NAICS 3333)
- Includes equipment for food processing, printing, and medical applications.
- The medical device segment has seen growth due to healthcare investments.
- Engine, Turbine, and Power Transmission Equipment Manufacturing (NAICS 3336)
- Produces gas and wind turbines, generators, and mechanical power systems.
- Increasing demand for energy-efficient systems and renewable energy projects.
- Other General-Purpose Machinery Manufacturing (NAICS 3339)
- Includes HVAC equipment, pumps, and fluid power systems.
- Benefiting from growth in commercial construction and industrial automation.
Technology and Automation in Machinery Manufacturing
The sector is at the forefront of technological innovation, integrating automation and advanced manufacturing techniques. Some of the most impactful developments include:
- Industrial robotics and smart factory systems that enhance efficiency.
- 3D printing for prototyping and small-scale custom parts production.
- AI-driven predictive maintenance to improve machinery lifespan and reduce downtime.
- Advanced sensor integration for remote monitoring and real-time performance analysis.
These advancements have led to a shift in workforce needs, increasing demand for workers skilled in programming, automation, and equipment maintenance.
Workforce Challenges
Despite steady employment levels, machinery manufacturing faces several workforce challenges:
- A shortage of skilled technicians, machinists, and automation specialists.
- Aging workforce, with many experienced workers nearing retirement.
- Rising raw material costs affecting production and job stability.
- The need for continuous retraining as machinery becomes more technologically advanced.
To address these issues, manufacturers are expanding training programs, partnering with technical schools, and adopting apprenticeship models to build a pipeline of skilled workers.
Geographic Distribution
Machinery manufacturing employment is concentrated in industrial regions with strong infrastructure and workforce capabilities:
- Midwest (Illinois, Ohio, Indiana, Michigan, Wisconsin) – A historic hub for machinery production, particularly industrial and construction equipment.
- South (Texas, Tennessee, Kentucky, Alabama, Georgia) – Growth in automotive and aerospace-related machinery manufacturing.
- West Coast (California, Washington, Oregon) – A leader in advanced robotics and semiconductor equipment production.
Future Outlook
Several key trends are expected to shape the future of machinery manufacturing:
- Growth in Automation and Smart Manufacturing
- Increased adoption of robotics, AI, and digital twins to improve efficiency.
- Expansion of Renewable Energy and Electric Power Equipment
- Demand for wind turbines, solar panel production equipment, and energy-efficient generators.
- Reshoring and Supply Chain Resilience
- Greater investment in domestic production to reduce dependence on foreign suppliers.
- Advanced Materials and Lightweight Machinery
- Development of high-strength, lightweight components for aerospace and electric vehicles.
- Workforce Development and Upskilling
- Investment in training programs to equip workers with digital and automation skills.
Machinery manufacturing remains a vital part of the U.S. economy, supporting multiple industries through the production of essential equipment and machinery. While employment has declined from historical levels, recent stability and technological advancements suggest a strong future. Continued investment in automation, workforce training, and domestic production will be crucial in maintaining competitiveness.
Computer and Electronic Product Manufacturing (NAICS 334)
The computer and electronic product manufacturing sector is a critical part of the U.S. technology industry, producing semiconductors, computers, communications equipment, and other high-tech products. This sector plays a major role in the global economy, supporting industries such as defense, telecommunications, and consumer electronics.
Employment Trends
Employment in computer and electronic product manufacturing has seen significant declines since the 1990s, largely due to offshoring, automation, and shifts in consumer demand. However, recent investments in domestic semiconductor production and advanced electronics manufacturing suggest a potential stabilization or resurgence.
- In 1990, the sector employed approximately 2 million workers.
- Employment peaked in the late 1990s before experiencing a steady decline.
- By 2010, employment had dropped below 1.2 million due to the outsourcing of electronics production to Asia.
- Recent government investments in semiconductor and chip manufacturing have helped slow the decline, with employment stabilizing at around 1 million in 2024.
The long-term trend has been one of decline, but the growing emphasis on domestic production of semiconductors and critical electronic components could reverse this pattern.
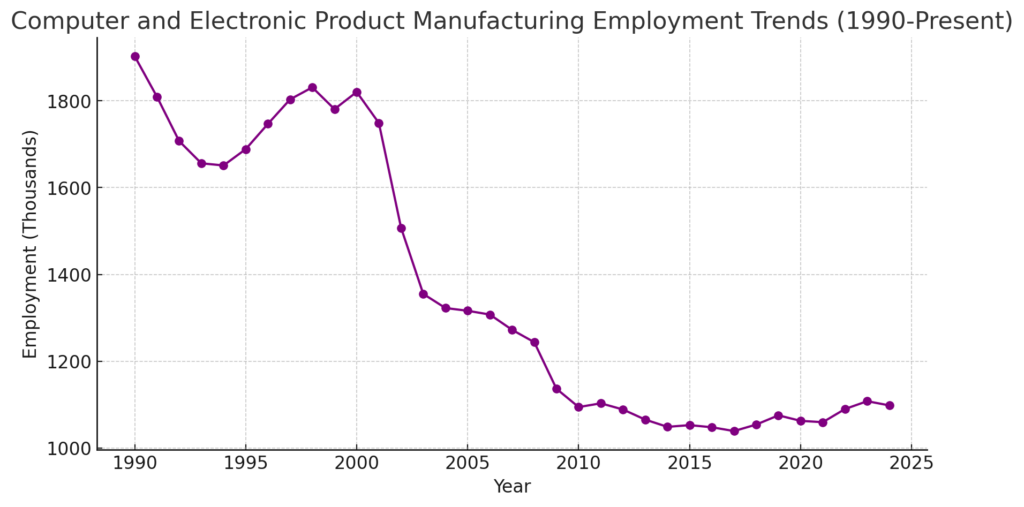
Industry Composition
The computer and electronic product manufacturing sector consists of several key industries:
- Semiconductor and Other Electronic Component Manufacturing (NAICS 3344)
- Produces microchips, circuit boards, and electronic components for computers, smartphones, and industrial applications.
- The CHIPS and Science Act is expected to create thousands of jobs in semiconductor fabrication.
- Computer and Peripheral Equipment Manufacturing (NAICS 3341)
- Includes the production of desktop computers, laptops, and storage devices.
- Employment in this segment has declined significantly due to offshore production.
- Communications Equipment Manufacturing (NAICS 3342)
- Produces networking hardware, fiber optics, and telecommunications devices.
- Growth in 5G infrastructure and broadband expansion is driving demand.
- Navigational, Measuring, Electromedical, and Control Instruments Manufacturing (NAICS 3345)
- Includes medical devices, aerospace navigation systems, and industrial sensors.
- This sector has remained relatively stable due to its high level of specialization.
- Audio and Video Equipment Manufacturing (NAICS 3343)
- Produces televisions, sound systems, and multimedia devices.
- Employment has declined as most consumer electronics production has moved to Asia.
Technology and Automation in Computer and Electronic Product Manufacturing
This sector is at the forefront of innovation, integrating automation, robotics, and artificial intelligence into manufacturing processes. Key technological advancements include:
- Advanced semiconductor fabrication, including extreme ultraviolet (EUV) lithography for high-performance chips.
- Automation in circuit board assembly, reducing reliance on manual labor.
- AI-driven quality control and predictive maintenance in semiconductor plants.
- 3D printing of electronic components for rapid prototyping and specialized applications.
While automation has replaced some traditional assembly jobs, it has also created new high-skill positions in semiconductor engineering, robotics maintenance, and process optimization.
Workforce Challenges
Despite the importance of this sector, there are several workforce challenges:
- A shortage of semiconductor engineers and highly skilled technicians.
- Competition from overseas manufacturers, particularly in Taiwan, South Korea, and China.
- Supply chain vulnerabilities, especially in rare earth materials required for electronics.
- The need for large-scale workforce training to support new semiconductor fabs being built in the U.S.
To address these issues, companies are investing in partnerships with universities, vocational training programs, and apprenticeship initiatives to develop a skilled workforce.
Geographic Distribution
Employment in computer and electronic product manufacturing is concentrated in high-tech hubs across the country:
- California (Silicon Valley) – The leading center for semiconductor design and high-tech manufacturing.
- Texas (Austin, Dallas, Houston) – A growing hub for semiconductor fabrication and electronics assembly.
- Arizona and New Mexico – Increasing investment in semiconductor foundries, including new Intel and TSMC plants.
- Oregon and Washington – Strong presence of semiconductor and computing equipment production.
- Massachusetts and New York – Focus on advanced medical devices, nanotechnology, and defense electronics.
Future Outlook
Several key trends will shape the future of computer and electronic product manufacturing:
- Expansion of Domestic Semiconductor Production
- The CHIPS and Science Act aims to increase U.S. semiconductor production and reduce reliance on Asian suppliers.
- Growth in Artificial Intelligence and High-Performance Computing
- Increased demand for AI chips and quantum computing hardware could create new opportunities in advanced electronics manufacturing.
- Reshoring of Critical Electronics Production
- Supply chain disruptions and national security concerns are driving efforts to bring back production of essential components.
- Green Technology and Energy-Efficient Electronics
- The development of low-power chips and sustainable manufacturing processes will shape the next generation of electronics.
- Continued Automation and Workforce Development
- As automation reduces the need for low-skill labor, the focus will shift to training workers for high-tech manufacturing roles.
Computer and electronic product manufacturing remains a strategically important sector, supporting critical industries such as defense, communications, and healthcare. While employment has declined over the past three decades due to offshoring, new investments in semiconductor production and advanced electronics manufacturing could lead to job growth in key areas. The future of this sector will depend on continued innovation, workforce training, and supply chain resilience.
Electrical Equipment, Appliance, and Component Manufacturing (NAICS 335)
The electrical equipment, appliance, and component manufacturing sector plays a key role in producing essential products for households, businesses, and industrial applications. This industry includes the manufacturing of household appliances, lighting, electrical components, batteries, and power distribution equipment.
Employment Trends
Employment in electrical equipment, appliance, and component manufacturing has experienced long-term declines due to offshoring and automation, but a notable resurgence has occurred since 2010.
- In 1990, the sector employed approximately 650,000 workers.
- Between 2000 and 2010, employment declined sharply due to global competition and outsourcing, reaching a low of around 350,000.
- Since 2010, employment has steadily increased, with the sector now employing approximately 400,000 workers in 2024.
- The growth since 2010 has been driven by reshoring efforts, increasing demand for electrical infrastructure, and investment in energy-efficient appliances and battery production.
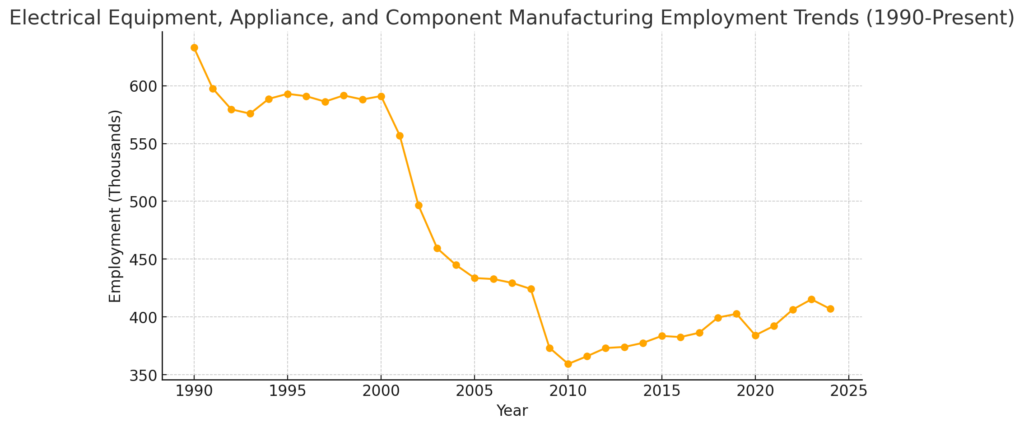
Industry Composition
The electrical equipment, appliance, and component manufacturing sector consists of several key industries:
- Electric Lighting Equipment Manufacturing (NAICS 3351)
- Produces lighting systems for homes, businesses, and industrial applications.
- Demand for LED and smart lighting systems has driven recent growth.
- Household Appliance Manufacturing (NAICS 3352)
- Includes refrigerators, washing machines, ovens, and small kitchen appliances.
- Increased consumer demand for energy-efficient and smart appliances has spurred innovation.
- Electrical Equipment Manufacturing (NAICS 3353)
- Produces transformers, switchgear, and power distribution systems.
- Investment in grid modernization and renewable energy infrastructure has boosted demand.
- Battery and Energy Storage Manufacturing (NAICS 3359)
- Focuses on lithium-ion batteries, industrial battery storage, and alternative energy solutions.
- Rapid expansion in electric vehicle (EV) and grid battery storage markets is fueling job creation.
Technology and Automation in Electrical Equipment Manufacturing
The sector has integrated advanced manufacturing technologies to improve efficiency and meet increasing demand for energy-efficient and smart products. Key advancements include:
- Robotics and automation in appliance assembly lines to improve quality and reduce costs.
- Internet of Things (IoT) integration in home appliances, creating demand for embedded systems engineers.
- AI-driven predictive maintenance in industrial electrical systems.
- Battery technology advancements, including solid-state batteries and improved lithium-ion production.
While automation has reduced the need for some traditional assembly roles, it has also created new job opportunities in robotics maintenance, electrical engineering, and AI-driven systems management.
Workforce Challenges
Despite recent growth, the industry faces several workforce challenges:
- A shortage of skilled workers in electrical engineering, automation, and battery production.
- Increased competition from Asian manufacturers in appliance and lighting equipment markets.
- The need for large-scale workforce training to support domestic battery production and electrical infrastructure expansion.
- Rising material costs, particularly for rare earth elements used in electrical components and batteries.
Manufacturers are addressing these challenges by expanding apprenticeship programs, investing in vocational training partnerships, and increasing automation efficiency to offset labor shortages.
Geographic Distribution
Employment in electrical equipment, appliance, and component manufacturing is concentrated in states with strong industrial and energy infrastructure:
- Midwest (Ohio, Indiana, Michigan, Illinois, Wisconsin) – Home to major appliance manufacturers and industrial electrical equipment producers.
- Southeast (Tennessee, Georgia, North Carolina, Kentucky, Alabama) – A growing hub for appliance production and battery manufacturing.
- Texas and California – Leading regions for energy storage manufacturing and electrical grid infrastructure.
- Nevada and Arizona – Emerging centers for lithium-ion battery production, driven by the growth of the EV industry.
Future Outlook
Several trends will shape the future of electrical equipment and appliance manufacturing:
- Expansion of Domestic Battery Production
- Increased investment in lithium-ion and next-generation battery technologies for EVs and energy storage.
- Growth in Smart Appliances and Connected Devices
- Rising consumer demand for IoT-enabled appliances will create new manufacturing and engineering jobs.
- Renewable Energy and Electrical Grid Modernization
- Upgrades to the power grid and the expansion of renewable energy will drive demand for transformers, switchgear, and energy storage systems.
- Reshoring of Appliance Manufacturing
- Supply chain disruptions and shifting trade policies may encourage companies to expand U.S.-based production.
- Automation and Workforce Development
- Increased use of robotics and AI will reshape manufacturing jobs, requiring a highly skilled workforce.
Electrical equipment, appliance, and component manufacturing remains a key sector in the U.S. economy, supporting energy infrastructure, consumer goods, and industrial applications. While employment has declined from historical peaks, the sector has shown steady growth since 2010, driven by advancements in smart appliances, battery technology, and electrical grid modernization. Continued investment in workforce training, automation, and domestic production will be essential for sustaining long-term competitiveness.
Transportation Equipment Manufacturing (NAICS 336)
The transportation equipment manufacturing sector is one of the largest and most dynamic industries in U.S. manufacturing. It includes the production of motor vehicles, aircraft, ships, railcars, and other transportation-related products that are essential to both domestic and global trade.
Employment Trends
Employment in transportation equipment manufacturing has fluctuated over the decades, with periods of decline due to economic downturns and industry restructuring, followed by strong growth in recent years.
- In 1990, the sector employed approximately 2 million workers.
- The early 2000s saw a decline in employment due to offshoring and automation.
- The Great Recession (2007–2009) hit the sector hard, causing employment to drop below 1.5 million.
- Since 2010, employment has surged, reaching nearly 1.8 million workers in 2024.
- This growth is largely attributed to a resurgence in domestic auto manufacturing, increased defense spending, and rising demand for electric vehicles (EVs) and aerospace products.
The trend suggests that despite global competition, domestic transportation equipment manufacturing remains a strong driver of U.S. job growth.
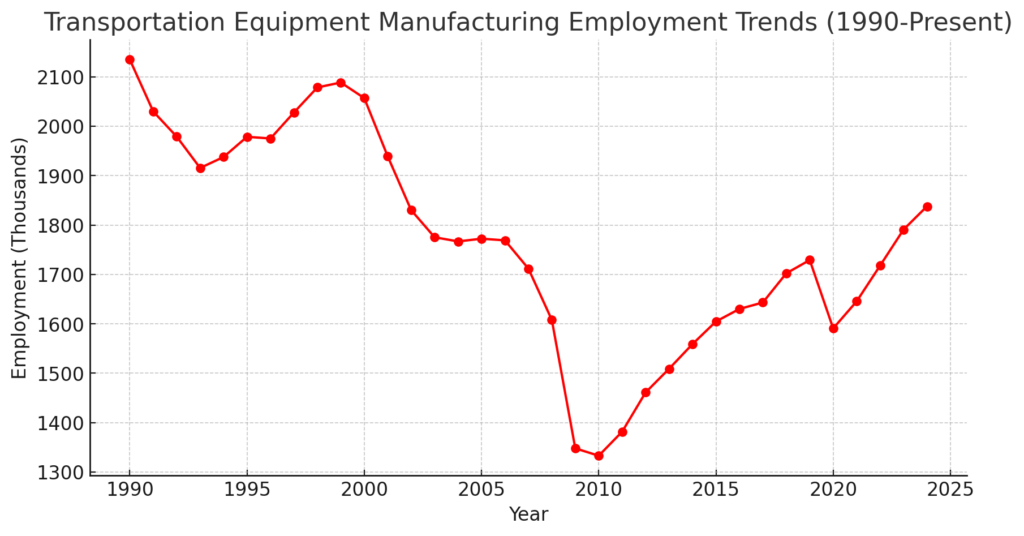
Industry Composition
The transportation equipment manufacturing sector consists of several major industries:
- Motor Vehicle Manufacturing (NAICS 3361)
- Includes passenger cars, light trucks, and commercial vehicles.
- The shift toward electric vehicles (EVs) has led to increased investments in domestic production.
- Motor Vehicle Body and Trailer Manufacturing (NAICS 3362)
- Produces bodies for trucks, buses, and trailers used in logistics and freight transport.
- Growth in e-commerce and delivery services has driven demand for specialized transport vehicles.
- Motor Vehicle Parts Manufacturing (NAICS 3363)
- Supplies components for the automotive industry, including engines, transmissions, and electronics.
- Supply chain disruptions during the COVID-19 pandemic led to efforts to localize production.
- Aerospace Product and Parts Manufacturing (NAICS 3364)
- Includes commercial aircraft, military jets, and space exploration vehicles.
- Strong demand from both commercial airlines and defense contracts is driving industry expansion.
- Railroad Rolling Stock Manufacturing (NAICS 3365)
- Produces locomotives, freight railcars, and passenger trains.
- Investments in rail infrastructure and high-speed rail projects could boost employment.
- Ship and Boat Building (NAICS 3366)
- Builds commercial ships, military vessels, and recreational boats.
- Defense and naval contracts have supported job stability in this subsector.
- Other Transportation Equipment Manufacturing (NAICS 3369)
- Includes motorcycles, all-terrain vehicles (ATVs), and specialty vehicles.
- Rising demand for off-road and recreational vehicles has driven steady growth.
Technology and Automation in Transportation Equipment Manufacturing
This industry has undergone significant technological advancements, reshaping how transportation equipment is designed and manufactured. Key developments include:
- Increased use of robotics and automation in vehicle assembly lines.
- Artificial intelligence (AI) for predictive maintenance and quality control.
- 3D printing for rapid prototyping and production of lightweight components.
- Expansion of electric vehicle (EV) production with new battery technologies.
- Smart manufacturing and digital twins to optimize efficiency in aerospace and automotive production.
While automation has led to job reductions in some areas, it has also created new opportunities in software engineering, robotics maintenance, and advanced materials manufacturing.
Workforce Challenges
Despite employment growth, the industry faces several workforce challenges:
- A shortage of skilled workers, particularly in advanced manufacturing and engineering roles.
- The transition to electric vehicles, requiring retraining of workers in battery and powertrain technology.
- Supply chain disruptions, particularly for semiconductors and raw materials.
- Increased global competition, with foreign automakers and aerospace firms expanding their production capacity.
To address these challenges, automakers and aerospace companies are investing in workforce training programs, apprenticeships, and partnerships with universities to develop a new generation of skilled technicians and engineers.
Geographic Distribution
Transportation equipment manufacturing is highly concentrated in regions with strong industrial infrastructure and workforce capabilities:
- Midwest (Michigan, Ohio, Indiana, Illinois, Missouri) – The traditional heart of the U.S. auto industry, home to major automakers and suppliers.
- Southeast (Kentucky, Tennessee, Alabama, South Carolina, Georgia) – A rapidly growing hub for automotive and aerospace manufacturing.
- West Coast (California, Washington, Arizona) – A center for aerospace and electric vehicle production.
- Texas and the Gulf Coast – Home to shipbuilding and aerospace defense manufacturing.
- Northeast (Pennsylvania, Connecticut, Massachusetts, New York) – Focused on high-tech aerospace and rail manufacturing.
Future Outlook
Several factors will shape the future of transportation equipment manufacturing:
- Growth in Electric Vehicles and Battery Manufacturing
- Automakers are investing billions in EV production, creating jobs in battery plants and powertrain development.
- Advancements in Aerospace and Space Exploration
- Increased investment in commercial space travel, satellites, and next-generation aircraft is driving aerospace manufacturing growth.
- Reshoring of Auto Parts and Semiconductor Manufacturing
- Efforts to reduce dependence on foreign suppliers, particularly for semiconductors, could boost domestic production.
- Expansion of High-Speed Rail and Public Transit Projects
- Government funding for rail infrastructure could lead to growth in passenger train and rolling stock manufacturing.
- Automation and Smart Manufacturing
- The continued adoption of robotics and AI in vehicle production will require a highly skilled workforce.
Transportation equipment manufacturing remains one of the largest and most dynamic sectors in U.S. manufacturing. The industry has experienced strong growth since 2010, driven by a combination of automotive expansion, aerospace investment, and technological advancements. As the transition to electric vehicles, smart manufacturing, and space exploration accelerates, the sector is likely to remain a key source of employment and economic growth in the coming decades.
Furniture and Related Product Manufacturing (NAICS 337)
The furniture and related product manufacturing sector produces a wide range of goods, including household furniture, office furnishings, mattresses, and specialized wood products. This industry has traditionally been a stronghold of U.S. manufacturing but has faced challenges from globalization, automation, and shifts in consumer preferences.
Employment Trends
Employment in furniture manufacturing has experienced long-term decline due to offshoring and automation, but there have been periods of stabilization, particularly in recent years.
- In 1990, the sector employed approximately 675,000 workers.
- Employment declined significantly from the early 2000s to 2010, reaching a low of around 350,000 due to outsourcing to Asia and Mexico.
- Since 2010, employment has stabilized, hovering around 350,000 to 400,000 workers.
- The COVID-19 pandemic caused temporary disruptions, but increased consumer spending on home goods helped sustain demand.
While employment remains below historical levels, there are signs of resilience, particularly in high-end and custom furniture production.
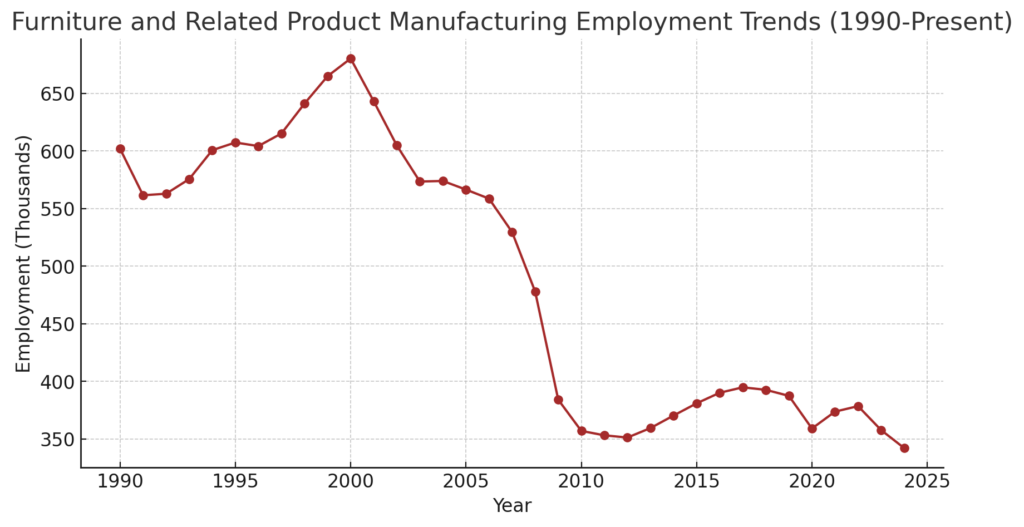
Industry Composition
The furniture and related product manufacturing sector consists of several key industries:
- Household and Institutional Furniture Manufacturing (NAICS 3371)
- Includes residential furniture, kitchen cabinets, and institutional furnishings.
- Strong demand for U.S.-made, custom, and sustainable furniture is supporting growth.
- Office Furniture Manufacturing (NAICS 3372)
- Produces desks, chairs, and workstations for commercial spaces.
- Demand has fluctuated due to the shift toward remote and hybrid work environments.
- Mattress and Blinds Manufacturing (NAICS 3379)
- Includes mattresses, window blinds, and other home furnishing products.
- Growth in online mattress sales and customizable home products is reshaping the industry.
Technology and Automation in Furniture Manufacturing
The furniture industry is integrating automation and digital technologies to improve production efficiency and meet shifting consumer preferences. Key innovations include:
- CNC machining and automated wood cutting, improving precision and reducing labor costs.
- 3D modeling and AI-driven design, enabling mass customization of furniture.
- Sustainable materials and eco-friendly production, responding to consumer demand for greener products.
- Automated upholstery and sewing systems, increasing efficiency in fabric-based furniture production.
While automation has led to job reductions in traditional woodworking roles, it has also created new opportunities in programming, robotics maintenance, and digital design.
Workforce Challenges
Despite its importance, the industry faces several workforce challenges:
- Shortage of skilled workers, particularly in woodworking, upholstery, and specialized furniture design.
- Competition from low-cost imports, particularly from China, Vietnam, and Mexico.
- Supply chain disruptions, affecting raw material availability and pricing.
- Fluctuating demand, with office furniture manufacturers adjusting to changing workplace trends.
To address these challenges, some companies are investing in workforce training, promoting domestic sourcing of materials, and expanding automation to improve efficiency.
Geographic Distribution
Furniture manufacturing employment is concentrated in states with strong traditions in woodworking and industrial production:
- North Carolina (High Point, Hickory, Thomasville) – The historical center of U.S. furniture production, specializing in high-end wood furniture.
- Mississippi and Tennessee – Major hubs for upholstered furniture and mattress production.
- Michigan and Indiana – Home to office furniture manufacturing and specialty furnishings.
- California and Texas – Growing centers for contemporary and eco-friendly furniture production.
Future Outlook
Several trends will shape the future of furniture and related product manufacturing:
- Growth in Custom and High-End Furniture
- Consumers are increasingly seeking U.S.-made, handcrafted, and customizable furniture.
- Sustainability and Eco-Friendly Materials
- The rise of green manufacturing is pushing companies to adopt sustainable woods, recycled materials, and low-emission production methods.
- E-commerce and Direct-to-Consumer Sales
- Online furniture brands are disrupting traditional retail channels, emphasizing home delivery and modular furniture solutions.
- Automation and Smart Manufacturing
- Investment in robotic manufacturing and AI-driven design could boost efficiency while preserving domestic production jobs.
- Reshoring of Furniture Production
- Rising labor costs in Asia and increased interest in “Made in USA” furniture could encourage some production to return to the U.S.
Furniture and related product manufacturing remains an important sector within U.S. manufacturing, despite challenges from offshoring and automation. While employment has declined from historical peaks, demand for high-quality, sustainable, and custom furniture is creating new opportunities for growth. The future of the industry will depend on investments in workforce training, sustainable production, and automation to remain competitive in the evolving global market.
Miscellaneous Manufacturing (NAICS 339)
The miscellaneous manufacturing sector is diverse, covering a wide range of specialized products that do not fall into traditional manufacturing categories. This includes medical equipment, jewelry, sporting goods, toys, and office supplies. While employment in this sector has fluctuated over time due to offshoring and automation, it has shown signs of resurgence since 2010, particularly in high-value and specialized manufacturing segments.
Employment Trends
Employment in miscellaneous manufacturing segments has undergone significant shifts over the past few decades.
- In 1990, the sector employed approximately 850,000 workers.
- Employment declined steadily from the early 2000s to 2010, dropping to around 600,000 due to offshoring and automation.
- Since 2010, employment has stabilized and begun to recover, reaching approximately 650,000 in 2024.
- The resurgence is driven by increased demand for medical devices, specialty manufacturing, and efforts to reshore production of high-value products.
While employment remains below its peak levels, this sector has demonstrated resilience, particularly in advanced manufacturing industries.
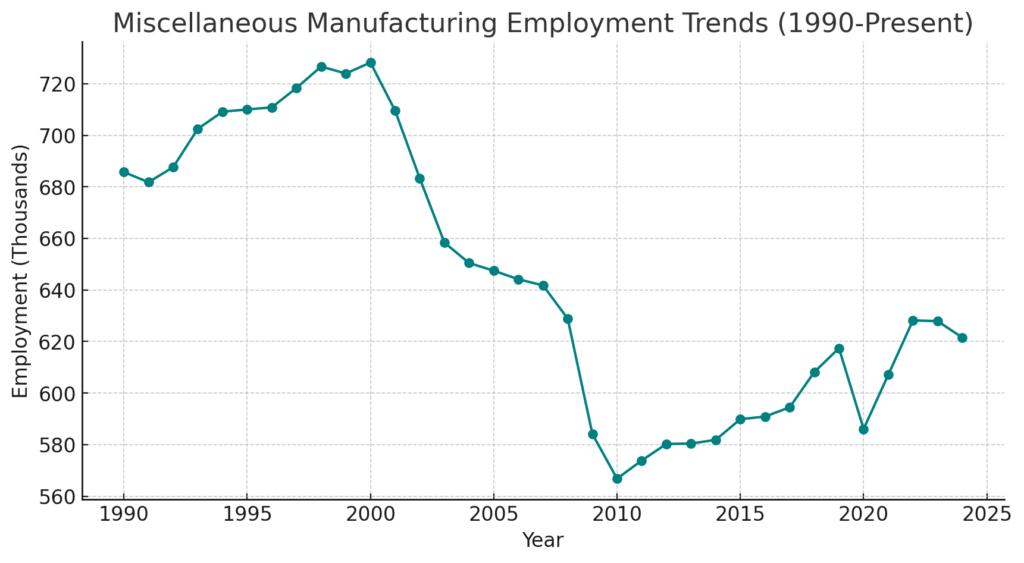
Industry Composition
The miscellaneous manufacturing sector consists of a few industry categorizations according to BLS:
- Medical Equipment and Supplies Manufacturing (NAICS 3391)
- Includes surgical instruments, prosthetics, dental equipment, and hospital supplies.
- Growth in healthcare spending and technological advancements have driven job creation.
- Other Miscellaneous Manufacturing (NAICS 3399)
- Covers jewelry, sporting goods, musical instruments, office supplies, and toys.
- Demand for domestically produced, high-quality, and custom products is growing.
Technology and Automation in Miscellaneous Manufacturing
Advancements in automation, robotics, and digital manufacturing are transforming the sector. Key innovations include:
- 3D printing for medical devices and custom products, allowing for rapid prototyping and low-volume production.
- Automation in jewelry and toy manufacturing, improving precision and efficiency while reducing production costs.
- Smart manufacturing for surgical instruments and prosthetics, integrating AI and robotics for high-precision medical equipment.
- Sustainable materials in office and sporting goods manufacturing, driven by consumer demand for eco-friendly products.
While automation has replaced some low-skill jobs, it has also created new opportunities in high-tech and precision manufacturing fields.
Workforce Challenges
Despite its growth, the sector faces several workforce challenges:
- A shortage of skilled technicians and engineers, particularly in medical device manufacturing.
- Competition from low-cost imports, particularly in sporting goods and office supplies.
- Supply chain disruptions, affecting access to raw materials such as rare metals used in medical and precision instruments.
- Need for retraining programs, as new manufacturing techniques require a higher level of technical expertise.
To address these challenges, companies are investing in workforce development, automation, and reshoring efforts to ensure a stable and skilled workforce.
Geographic Distribution
Manufacturing employment in these miscellaneous industry sectors is spread across various regions, depending on the specific industry:
- Minnesota and Massachusetts – Major hubs for medical equipment and device manufacturing.
- California and Texas – Centers for high-tech specialty manufacturing, including sporting goods and musical instruments.
- Rhode Island and New York – Historical centers for jewelry and small-scale luxury goods production.
- Midwest (Illinois, Michigan, Ohio, Indiana) – Home to office supply and specialty component manufacturing.
Future Outlook
Several trends are expected to shape the future of manufacturing in these subsectors:
- Expansion of Medical Device and Healthcare Equipment Manufacturing
- Aging populations and advances in healthcare technology will drive demand for prosthetics, diagnostic equipment, and surgical instruments.
- Growth in Additive and Custom Manufacturing
- 3D printing and smart factories will allow for greater customization in niche products such as sporting goods and musical instruments.
- Reshoring of High-Value Specialty Products
- Increasing focus on domestic production of medical supplies and specialty goods to improve supply chain security.
- Sustainability and Eco-Friendly Manufacturing
- Rising consumer demand for sustainable office supplies, recyclable sporting goods, and ethically sourced jewelry.
- Integration of Smart Manufacturing and AI
- Adoption of AI-driven quality control and digital twin simulations will enhance efficiency and reduce waste in precision manufacturing.
The remainder of US manufacturing remains a vital sector, covering a broad range of specialized industries that support healthcare, recreation, and consumer products. While employment has declined from historical levels, the sector is experiencing renewed growth, particularly in medical equipment and high-value specialty products. Continued investment in automation, workforce development, and sustainable production will be key to maintaining long-term competitiveness.
The State of American Manufacturing Jobs and the Path Forward
Manufacturing remains a cornerstone of the U.S. economy, providing millions of jobs across diverse industries. However, the sector has undergone dramatic changes over the past several decades, shaped by forces such as globalization, automation, trade policy, and shifting workforce demographics.
From its peak in 1979 with nearly 20 million manufacturing jobs to its subsequent decline due to offshoring, trade liberalization, and technological advancements, the industry has faced significant challenges. Despite these shifts, manufacturing employment has shown resilience in recent years, with domestic reshoring efforts, government incentives, and technological advancements creating new opportunities.
The data examined in this paper highlights the uneven distribution of manufacturing employment across subsectors. Industries such as food manufacturing, transportation equipment, and fabricated metal products continue to employ a substantial portion of the workforce, while others, like textile, apparel, and leather manufacturing, have seen significant declines due to foreign competition.
Several critical factors will determine the future trajectory of manufacturing jobs in the U.S.:
- Technology and Workforce Development – As automation continues to reshape the industry, there is an urgent need for skilled labor in areas like robotics, AI, and advanced manufacturing. Expanding vocational training, apprenticeship programs, and industry partnerships with educational institutions will be key to bridging the skills gap.
- Trade Policy and Global Competition – The de minimis loophole, import tariffs, and trade agreements will continue to shape manufacturing employment. Ensuring that domestic producers remain competitive against foreign imports—especially from low-cost manufacturing hubs like China—will be essential for sustaining job growth.
- Government Investment and Industrial Policy – Recent policies, such as the CHIPS and Science Act and the Inflation Reduction Act (IRA), aim to revitalize domestic production in strategic industries like semiconductors, clean energy, and electric vehicles. The success of these initiatives will play a crucial role in determining the long-term stability of the manufacturing workforce.
- Regional Job Growth and Reshoring Efforts – The geographic distribution of manufacturing jobs has shifted, with growth in the Southeast and Southwest and declines in traditional Rust Belt states. Policymakers must consider infrastructure investments, workforce incentives, and regional economic development strategies to support continued reshoring efforts.
Final Thoughts
Lots of manufacturing jobs are disappearing, but they are also evolving. While low-skill, labor-intensive roles have declined due to automation and global competition, the sector continues to generate high-value, technical jobs that require specialized skills. The challenge now is ensuring that the U.S. workforce is prepared for this shift.
By investing in workforce training, modernizing trade policies, and strengthening domestic supply chains, the U.S. can secure its position as a global leader in advanced manufacturing while preserving the sector’s role as a pillar of economic stability and job creation. The future of American manufacturing depends not only on technological progress, but also on the policies and workforce strategies that will define the next generation of manufacturing jobs.